Ultrasonic Vs Pressure Water Level Measurement: Which Method is More Reliable?
By:Admin
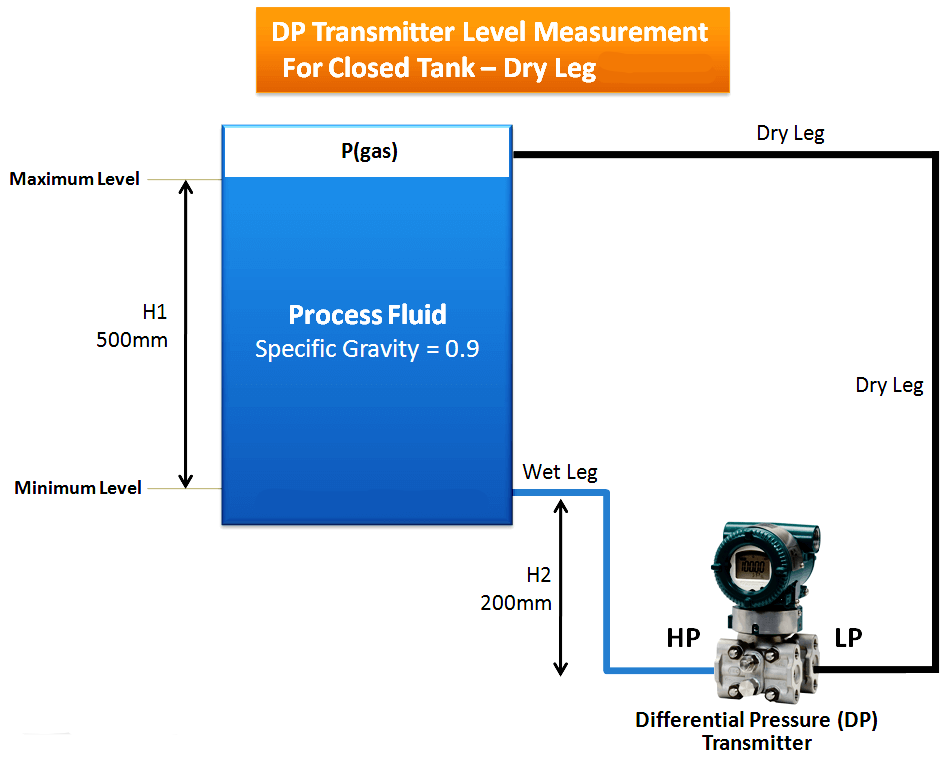
Water Level Measurement: Ultrasonic vs. Pressure-based
Accurately measuring water levels is essential in a variety of applications, such as water treatment facilities, irrigation systems, and flood detection systems. Traditionally, water level measurement has been done using pressure-based sensors, which measure the water pressure at a certain depth. However, ultrasonic sensors are becoming increasingly popular due to their many benefits over pressure-based sensors.
One major advantage of ultrasonic sensors is their accuracy. Unlike pressure-based sensors, which can be affected by changes in temperature, ultrasonic sensors measure the time it takes for sound waves to travel from the sensor to the water surface and back. This means that ultrasonic sensors can provide highly accurate measurements regardless of environmental fluctuations.
Another benefit of ultrasonic sensors is their versatility. Ultrasonic sensors can be used in a wide range of applications, including open channels, tanks, and wells. They can also measure water levels with high accuracy over long distances, making them ideal for large bodies of water or difficult-to-reach areas.
Ultrasonic sensors are also more reliable than pressure-based sensors. Pressure-based sensors are more prone to clogging, which can affect their accuracy. On the other hand, ultrasonic sensors usually only require periodic cleaning to maintain their accuracy.
In addition, ultrasonic sensors are more cost-effective over the long term. Pressure-based sensors require regular calibration and maintenance, which can be costly. Ultrasonic sensors, on the other hand, have a longer lifespan and require less maintenance, making them a more cost-effective option in the long run.
One company that offers ultrasonic water level measurement solutions is {}. With over {} years of experience in the industry, {} provides a range of ultrasonic sensors that are designed for various applications. Their sensors are highly accurate and reliable, making them ideal for a wide range of industries, including water management, agriculture, and environmental monitoring.
In conclusion, ultrasonic sensors offer a range of benefits over pressure-based sensors for water level measurement. They offer greater accuracy, versatility, reliability, and cost-effectiveness, making them an increasingly popular choice for a wide range of applications. If you are in need of water level measurement solutions, consider exploring the benefits of ultrasonic technology and contacting {} for more information.
Company News & Blog
Inexpensive Inline Sensors Can Provide Concentration Measurements for Optimal Control of Key Components
: How to Obtain Concentration Measurements from Common Inline SensorsControlling key components' concentration is an essential part of many industrial processes. However, obtaining accurate concentration measurements is often challenging, especially when dealing with hazardous or challenging substances. Fortunately, there is a simple solution - relatively inexpensive inline measurements that can provide precise concentration measurements with the right conditions. In this blog, we will examine how to obtain concentration measurements from common inline sensors and how they can benefit industrial processes.The first type of inline sensor that can be used for concentration measurement is an inline pH meter. These meters work by measuring the acidity or alkalinity of a solution based on its hydrogen ion concentration. This information can be used to determine the concentration of various substances in the solution, such as acids or bases. Inline pH meters are often used to monitor the concentration of chemicals in the wastewater treatment industry. They are also common in food and beverage production, where they can be used to monitor acidity levels in products such as beer and yogurt.To obtain accurate concentration measurements using an inline pH meter, several conditions must be met. First, the pH meter must be calibrated correctly to ensure that it is providing accurate readings. This involves adjusting the meter to the appropriate pH range for the solution being measured and ensuring that the sensor is properly cleaned and maintained. Second, the solution being measured must be free from contaminants that could affect the pH reading, such as oils or other chemicals. Finally, the pH meter must be installed correctly, with the sensor placed in the appropriate location to provide an accurate reading.The second type of inline sensor that can be used for concentration measurement is a conductivity meter. These meters work by measuring the electrical conductivity of a solution, which is directly proportional to the concentration of dissolved solutes in the solution. Conductivity meters are commonly used in the pharmaceutical and chemical industries, where they are used to measure the concentration of ionic compounds such as salts and acids.To obtain accurate concentration measurements using an inline conductivity meter, several conditions must be met. First, the meter must be calibrated correctly to ensure that it is providing accurate readings. This involves adjusting the meter to the appropriate conductivity range for the solution being measured and ensuring that the electrodes are properly cleaned and maintained. Second, the solution being measured must be free from contaminants that could affect the conductivity reading, such as oils or other chemicals. Finally, the conductivity meter must be installed correctly, with the electrodes placed in the appropriate location to provide an accurate reading.Overall, using inline sensors to obtain concentration measurements is an effective and cost-effective way to monitor industrial processes. By ensuring that the sensors are calibrated correctly, the solution is free from contaminants and installed correctly, accurate concentration measurements can be obtained, allowing for optimal process control and optimization.In conclusion, obtaining accurate concentration measurements is an essential part of many industrial processes. Inline sensors, such as pH meters and conductivity meters, are effective and relatively inexpensive tools for obtaining these measurements, provided the correct conditions are met. By incorporating inline sensors into industrial processes, companies can optimize their processes, reduce waste and potentially increase profitability.
New Level Transmitter Technology Eliminates Impulse Lines and Capillary Tubes
In today’s modern process industries, level measurement is an essential part of monitoring and controlling the fluid level of tanks, vessels, and other containers. There are several ways to measure the level of fluid, including ultrasonic, radar, and differential pressure (DP) level transmitters. Among these, DP level transmitters have been widely used and offer excellent accuracy and reliability.In traditional DP level transmitters, impulse lines and capillary tubes were used to transmit the pressure difference between the liquid and the reference pressure to the measuring cell. However, these lines and tubes were prone to clogging, leakage, or freezing, which caused inaccurate measurements and increased maintenance costs.Thanks to technological advancements, DP level transmitters have evolved to overcome the limitations of traditional designs. Modern DP level transmitters do not use impulse lines or capillary tubes, making them easier to install, operate, and maintain. Instead, they use electronic remote seals or direct-mount seals, which eliminate the need for long tubing runs.Electronic remote seals use a digital signal processor (DSP) to convert the pressure signals from the remote seal into a standard output signal. The remote seal can be located up to 328 feet away from the transmitter, allowing it to be installed in harsh or hazardous environments. The signal is transmitted via two-wire technology, eliminating the need for additional wiring and reducing installation costs.Direct-mount seals can be mounted directly on the process connection of the transmitter, eliminating the need for impulse lines or capillary tubes. They are available in a range of materials and designs to meet different process requirements. Direct-mount seals are easy to install, and they do not require additional calibration or adjustment.Capillary level transmitters offer an alternative solution that eliminates the need for impulse lines and capillary tubes. Instead, they use a single capillary tube to connect the process connection to the measuring cell. The capillary tube is filled with a special fluid that transmits the pressure difference to the cell. Capillary level transmitters are accurate and reliable, and they offer excellent stability over a wide range of process temperatures and pressures.In conclusion, DP level transmitters have come a long way since the traditional designs that used impulse lines and capillary tubes. Modern transmitters offer several solutions that eliminate the need for these lines, making them more reliable, accurate, and easy to maintain. Capillary level transmitters offer additional advantages that make them ideal for certain process applications. When selecting a DP level transmitter, it’s important to consider the specific requirements of the process and choose the best solution that meets those needs.
Newest Air Pressure Sensor Products List from Chinese Manufacturers and Suppliers in 2019
Manufacturers, Air Pressure Sensor Factory, China Air Pressure Sensor ProductsAir pressure sensors are vital components in a wide range of industrial applications. These sensors measure air pressure and provide essential information that is used to control various processes. With the vast range of applications, high-quality air pressure sensors are in high demand.China has become a significant player in the production of air pressure sensors globally. Chinese air pressure sensor manufacturers have earned a reputation for producing high-quality, reliable sensors at competitive prices. The following are some of the latest air pressure sensor products from China's top manufacturers.1. Digital Air Pressure SensorThis air pressure sensor is designed for high-precision, digital pressure measurement. It features a compact design, high accuracy, and a wide measuring range. This sensor is ideal for applications that require long-term stability, high accuracy, and low power consumption.2. Industrial Air Pressure SensorThis industrial air pressure sensor is designed for use in harsh industrial environments. It features a rugged design that can withstand extreme temperatures, humidity levels, and vibration. This sensor is ideal for use in applications such as HVAC systems, hydraulic systems, and automotive manufacturing.3. Medical Air Pressure SensorThis medical air pressure sensor is designed for use in medical equipment such as ventilators, anesthesia machines, and blood pressure monitors. It features high accuracy, low power consumption, and a compact design. This sensor is ideal for applications that require precise and reliable pressure measurements.4. Smart Air Pressure SensorThis smart air pressure sensor is designed for use in applications such as smart homes, wearable devices, and IoT devices. It features a wireless connection and can be remotely monitored and controlled using a smartphone app. This sensor is ideal for applications that require real-time monitoring and control.China's air pressure sensor manufacturers are committed to producing high-quality products that meet the rigorous demands of industry. From digital sensors to smart sensors, these manufacturers offer a wide range of products that cater to different applications. With competitive prices and reliable products, China's air pressure sensor industry is poised for continued growth in the years to come.
Find the Right Flow Meters for Your Application at Instrumart" -> "Discover Flow Meters Tailored to Your Needs
IntroductionFlow meters are instrumental devices in the field of fluid measurement and management, used to measure the volumetric flow rate or mass flow rate of a fluid. They are extensively used in a variety of industries such as oil and gas, water treatment, food and beverage, pharmaceuticals, and chemical processing. In this article, we will explore the concept of area flow meters.What are Area Flow Meters?Area flow meters are a type of flow meters that determine the flow rate of a fluid by measuring the cross-sectional area of the fluid in a predefined flow channel. These types of flow meters are also known as variable area flow meters or rotameters.Area flow meters work based on the principle known as the "upward force of flow." This principle states that a fluid flowing in a vertical tube will experience an upward force proportional to the mass flow rate. As the flow rate increases, the cross-sectional area of the tube increases proportionally. Therefore, the position of an indicator within the tube gives an indication of the flow rate.Types of Area Flow MetersThere are several types of area flow meters, each with its own advantages and limitations.Rotameters: As mentioned earlier, rotameters are the most common type of area flow meters. They are typically designed with a vertical glass or plastic tube and a float that moves up and down inside the tube. The position of the float within the tube indicates the flow rate of the fluid.Flow Nozzles: Flow nozzles are used to measure the flow rate of liquids or gases in a pipe. They feature a constriction in the flow path, which causes a pressure drop across the nozzle. By measuring the pressure drop, one can determine the flow rate of the fluid.Venturi Meter: Venturi meters are similar to flow nozzles, but they use a gradual or tapered constriction in the flow path instead. This creates a low-pressure zone, which can then be used to calculate the flow rate.Pitot Tubes: Pitot tubes are used to measure the velocity of a fluid. They feature a probe that is inserted into the fluid stream perpendicular to the flow direction. As the fluid strikes the probe, it is slowed down, creating a pressure difference between the front and the back of the probe. By measuring this pressure difference, the velocity of the fluid can be calculated.Advantages of Area Flow MetersArea flow meters have several advantages over other types of flow meters, such as:Simple Design: Area flow meters generally have a relatively simple design, which makes them less expensive than other types of flow meters.Suitable for Wide Range of Fluids: They are suitable for use with a wide variety of fluids, including liquids and gases.Low Maintenance: They have no moving parts, making them less prone to wear and tear and require less maintenance.Limitations of Area Flow MetersDespite their advantages, area flow meters have some limitations, including:Limited Range: Area flow meters have a limited range of flow rates they can measure, typically between 10:1 and 20:1.Reliance on Accuracy Factors: Area flow meters' accuracy is reliant on the thickness, viscosity and temperature of the fluid being measured.ConclusionArea flow meters are an essential tool used in a wide range of applications to measure fluids' flow rates. They are simple in design, effective and versatile, making them ideal for use in several industries. Whether you are measuring liquids or gases, area flow meters can provide accurate and reliable flow rate measurements, making them an indispensable tool in the world of fluid measurement.
NIVEL Offers High-Quality Street Legal Golf Carts for Sale: Gas, Electric & Lithium Ion Powered!
Title: Sensor Ultrasonico Nivel: Unlocking the Future of Street Legal Golf CartsIntroduction:In recent times, the demand for street-legal golf carts has surged dramatically. This influx in popularity can be attributed to their versatility, eco-friendliness, and overall efficiency. Among the wide array of street-legal golf carts available for sale, the emergence of ultrasonic level sensors has taken these carts to an entirely new level. In this blog, we will delve into the world of sensor ultrasonico nivel and explore why it has become an indispensable feature in modern street-legal golf carts.Section 1: The Power of Street-legal Golf Carts:Street-legal golf carts have rapidly gained momentum due to their convenience and excellent eco-credentials. With the ability to navigate public roads safely, these golf carts have become popular for not only golf course transportation but also for a variety of recreational and utility purposes. Whether it's running errands in residential areas, exploring leisure areas, or even commuting short distances, street-legal golf carts offer an exciting and emission-free alternative.Section 2: The Role of Ultrasonic Level Sensors:Sensor ultrasonico nivel, or ultrasonic level sensors, have revolutionized the world of street-legal golf carts. These sensors utilize ultrasonic technology to accurately measure and assess the distance between objects and the golf cart. Equipped with both transmitting and receiving capabilities, ultrasonic level sensors send high-frequency sound waves, which bounce off any obstacles in their path.Section 3: Unleashing Safety and Control:One of the key advantages of sensor ultrasonico nivel in street-legal golf carts is enhanced safety and control. With the ability to detect obstacles, such as other vehicles, pedestrians, or even stationary objects, ultrasonic level sensors provide golf cart drivers with valuable information to make informed decisions. These sensors help avoid collisions, mitigate accidents, and prevent damage to property, ensuring a smoother and safer ride for both the driver and other road users.Section 4: Effortless Maneuvering and Parking:In addition to safety features, sensor ultrasonico nivel significantly improves the maneuverability and parking capabilities of street-legal golf carts. These sensors assist drivers by providing accurate real-time feedback about the proximity to surrounding objects. With precise distance measurements, golf cart drivers can navigate through tight spaces, narrow paths, or crowded areas effortlessly, resulting in stress-free parking experiences.Section 5: Energy Efficiency and Optimization:Street-legal golf carts equipped with ultrasonic level sensors also enjoy superior energy efficiency. With the innate ability to detect obstacles, these sensors allow for optimal driving paths, reducing unnecessary acceleration, braking, and steering. By providing a clearer vision of the road ahead, golf cart drivers can tailor their driving patterns for maximum efficiency, ultimately extending battery life and reducing energy consumption.Section 6: The Future of Sensor Ultrasonico Nivel:As the popularity of street-legal golf carts continues to grow, the future of sensor ultrasonico nivel presents numerous exciting opportunities. The ongoing advancements in technology offer the potential for even more sophisticated sensor systems that can incorporate features like machine learning, adaptive cruise control, and autonomous driving capabilities. These innovative developments will undoubtedly elevate the driving experience to a whole new level, emphasizing safety, convenience, and sustainability.Conclusion:The integration of sensor ultrasonico nivel into street-legal golf carts has indubitably transformed the way we perceive and use these vehicles. Enhancing safety, control, maneuverability, and energy efficiency, ultrasonic level sensors have become an essential component of modern golf cart technology. With the ongoing advancements and endless possibilities, the future of sensor ultrasonico nivel promises to shape the landscape of street-legal golf carts and ensure a brighter and greener future ahead.
Why Use 4-20 mA Current Loop for Industrial Transducers?
Current Loop to Voltage Converter (4-20mA to 0-3.3V/0-5V/0-10V) – Why is 4-20mA Current Loop Important for Industrial Applications?In industrial environments, it is essential to have accurate and reliable measurements of various parameters to ensure optimal performance and safety of machinery and equipment. These parameters can include temperature, pressure, flow rate, and other physical variables that need to be transmitted from the sensor or transducer to a control system or display device.While there are different methods of transmitting sensor data, industrial-grade transducers often use current signals to transmit data through a phenomenon known as a 4-20mA Current Loop. This technique has been widely used in the industry for many years due to its benefits of accuracy, reliability, and simplicity.In this article, we will explore the reasons why 4-20mA Current Loop is crucial in industrial applications and how it works. We will also look at how Current Loop to Voltage Converters can be used to convert these current signals to voltage levels that can be easily read by standard controllers and data acquisition systems.Why Use Current Signals for Industrial Applications?In industrial environments, there are various sources of electrical noise and interference that can affect the accuracy and reliability of sensor data. These can include electromagnetic fields from motors, transformers, and power supplies, as well as radio-frequency interference from wireless devices and other sources.One of the advantages of using current signals for transmitting data is their immunity to electrical noise and interference. Since the current flows through a closed loop circuit, any external noise will be cancelled out by the loop's resistance. Therefore, even in noisy environments, the current signal can still provide reliable and accurate data measurement.Another advantage of using current signals is their ability to travel long distances without significant signal loss. Unlike voltage signals, which can be affected by capacitance and resistance in the transmission line, current signals generate a voltage drop that is proportional to the resistance of the loop. As a result, the signal can be transmitted over long distances without significant attenuation.How Does the 4-20mA Current Loop Work?The 4-20mA Current Loop is a simple two-wire circuit that connects the sensor or transducer to the control system or display device. The circuit consists of an external power supply, usually 24V DC, a current source, and a load resistor.The sensor or transducer generates an analog signal that is proportional to the physical parameter being measured. This signal is then fed into the current source, which generates a current that is proportional to the signal. For example, if the sensor signal is 50% of the full-scale value, the current source generates 12mA (50% of the 4-20mA range).The current then flows through the load resistor and returns to the current source. The voltage drop across the load resistor is proportional to the current and therefore proportional to the sensor signal. This voltage drop can be measured by the control system or display device and converted back to a physical value.Using a Current Loop to Voltage ConverterWhile the 4-20mA Current Loop provides accurate and reliable data transmission, most standard controllers and data acquisition systems are designed to read voltage signals. Therefore, a Current Loop to Voltage Converter is often required to convert the current signal to a voltage level that can be easily read by these devices.A Current Loop to Voltage Converter is a simple interface circuit that connects between the current loop and the controller or data acquisition system. It typically consists of a shunt resistor, an operational amplifier, and a voltage regulator.The shunt resistor is connected in series with the loop and generates a voltage drop that is proportional to the current in the loop. The operational amplifier amplifies this voltage drop and provides a high-impedance output that can be easily read by the controller or data acquisition system.ConclusionIn summary, the 4-20mA Current Loop is a widely used data transmission technique in industrial applications due to its accuracy, reliability, and immunity to electrical noise and interference. The Current Loop to Voltage Converter provides a simple and effective solution for converting these current signals to voltage levels that can be easily read by standard controllers and data acquisition systems.As industries continue to demand more reliable and accurate data transmission, the 4-20mA Current Loop will continue to play a vital role in delivering this data. Future Electronics Egypt offers a wide range of Current Loop to Voltage Converters and other industrial-grade components to help customers meet their data transmission needs.
Top-rated Supplier and Manufacturer of Radar Level Indicators in China
Understanding Radar Level Indicators and Their Importance in IndustriesIndustries such as petroleum, chemical, food processing, and utilities require an efficient and accurate way of measuring the level of liquids and solids in various containers and tanks. This is where the radar level indicator comes in. Radar level indicators are essential instruments that help in measuring the level of liquid, solids, and sludge in tanks, vessels, and silos accurately. These instruments utilize the latest technology to deliver accurate, reliable, and real-time information about the level of fluids, liquids, and solids in storage tanks.What is a Radar Level Indicator?Radar level indicators are devices with advanced electronic systems used to measure the level of liquids and solids in tanks and silos. These instruments work by transmitting electromagnetic waves that travel down to the surface of the stored product in the tank. The electromagnetic waves reflect back to the radar level indicator's antenna, which measures the time it takes for the waves to return. This process helps determine the distance between the surface of the liquid or solid and the level sensor.Types of Radar Level IndicatorsThere are two main types of radar level indicators: Guided Wave Radar (GWR) and Non-Contact Radar (NCR). The main differences between these two types lie in their mode of operation.1. Guided Wave RadarGuided Wave Radar (GWR) level indicators work by sending high-frequency electromagnetic waves down a probe (or waveguide) inserted into the tank or vessel. The electromagnetic waves move down the probe until they reach the liquid or solid product. The waves reflect back to the probe, which measures the time it takes for the waves to return. This data helps determine the level of product in the tank.GWRs are versatile and can measure the level of a wide range of liquids and solids, from water to molten metal. They are also suitable for high-temperature and high-pressure applications.2. Non-Contact RadarNon-Contact Radar (NCR) level indicators use a horn antenna to send out electromagnetic waves towards the product's surface. The waves penetrate the product, reflect back to the antenna and are then measured. NCRs are ideal for measuring the level of substances that are not conductive, such as powders and solids.Benefits of Using Radar Level Indicators1. Increased efficiencyRadar level indicators provide a real-time view of the level of product in the tank or vessel. This data helps operators to maintain the optimum level of product, reducing overfilling or underfilling.2. Improved Safety and Environmental ProtectionOverfilling of tanks and vessels can lead to catastrophic consequences, such as spills, which can result in environmental degradation and accidents. Radar level indicators provide reliable and real-time information that can help prevent these situations.3. VersatilityRadar level indicators are versatile and can measure the level of a wide range of liquids and solids, from water to molten metal. This ensures that industries can use the instruments in various applications.4. Cost SavingsIndustries that use radar level indicators can save on costs associated with material waste and production downtime. Operators can also reduce equipment damage due to overfilling and avoid costly repairs.ConclusionRadar level indicators are essential instruments that provide accurate and reliable measurements of the level of liquids and solids in tanks, silos, and vessels. Industries can use these devices in various applications, thus ensuring efficient product management. Additionally, radar level indicators promote environmental protection and safety by preventing overfilling of tanks and vessels. Investing in radar level indicators can lead to increased efficiency, reduced costs, and improved safety in industries.
Hydrostatic Level Probe for Wastewater - Piezoresistive and Differential Pressure Options
A hydrostatic level probe is an essential instrument used to measure the level of liquids, particularly wastewater. It is an innovative solution that provides accurate measurements in submerged environments and helps monitor the liquid levels in tanks and vessels.The hydrostatic level probe works on the basis of hydrostatic pressure principles. It measures the pressure exerted by the liquid on the bottom of the tank. This pressure reading is then transformed into a level measurement that helps operators optimize their wastewater treatment systems.There are several types of hydrostatic level probes available in the market, including piezoresistive, differential pressure, and submersible level sensors. They vary in terms of their technology, construction, measurement range, and accuracy. One of the most popular options is the Piezo As Hydrostatic Level Probe.The Piezo As Hydrostatic Level Probe is an advanced and reliable liquid level measuring instrument that uses piezoresistive technology for accurate measurements in challenging industrial environments. The probe consists of a high-precision ceramic measuring cell with fully integrated electronics that deliver reliable and accurate results.The probe is designed to withstand harsh conditions, including corrosive and abrasive substances, and can operate at high temperatures and pressures. It is suitable for use in various applications, such as water and wastewater treatment, chemical processing, and oil and gas refining.With a measurement range of up to 1,000 meters and an accuracy of up to 0.1 percent, the Piezo As Hydrostatic Level Probe is an ideal choice for industrial liquid level measurement applications. The probe is easy to install, maintain, and integrate into existing control systems, and it provides reliable and accurate measurements even in challenging environments.In conclusion, wastewater treatment is critical to the environment and human health, and accurate level measurement is essential to optimize the process. The hydrostatic level probe, such as the Piezo As Hydrostatic Level Probe, is an efficient, cost-effective, and reliable solution that can deliver accurate measurements and help operators ensure the smooth operation of their wastewater treatment systems.
Top Chinese Manufacturer with 20 Years of Experience in Silicon Pressure Sensors
: Benefits and ApplicationsPressure sensors are essential components in many industrial applications, as they help monitor and regulate pressure in a variety of environments. When it comes to silicon pressure sensors, they are among the most commonly used because of their high accuracy, low power consumption, and compact size. Silicon pressure sensors are designed to detect changes in pressure and provide an electrical output, making them ideal for use in a wide range of industries, including automotive, medical, aerospace, and manufacturing. In this article, we will explore the benefits and applications of silicon pressure sensors.Benefits of Silicon Pressure SensorsAccuracyOne of the primary benefits of silicon pressure sensors is their high accuracy. They can provide precise readings of pressure changes, making them ideal for critical applications such as aerospace and medical industries, where precision and accuracy are paramount.Compact SizeSilicon pressure sensors are also highly compact, making them easy to install in tight spaces. They are typically small enough to fit within electronic devices, which is why they are commonly used in medical devices and other portable equipment.Low Power ConsumptionSilicon pressure sensors require minimal power to function. This makes them ideal for battery-operated devices, such as wireless sensors and portable equipment, where energy conservation is important.DurabilitySilicon pressure sensors are highly durable and can withstand harsh environments. They can function in high temperatures, rugged locations, and corrosive environments without losing their accuracy. This makes them ideal for use in the automotive industry or other areas where sensors are exposed to harsh conditions.Applications of Silicon Pressure SensorsAerospace IndustrySilicon pressure sensors are widely used in the aerospace industry to monitor pressure changes in critical systems, such as fuel injection, hydraulic systems, and pneumatic systems. These sensors play a vital role in ensuring the safety and reliability of aerospace equipment.Automotive IndustrySilicon pressure sensors are used in the automotive industry to monitor fuel pressure, oil pressure, and transmission pressure. These sensors provide essential data to control engine performance, improve fuel economy, and enhance driver safety on the road.Medical IndustrySilicon pressure sensors are widely used in medical devices to monitor vital signs such as blood pressure, heart rate, and respiratory rate. Medical devices such as blood pressure monitors, ventilators, and infusion pumps use silicon pressure sensors to provide accurate and reliable data.Manufacturing IndustrySilicon pressure sensors are used in the manufacturing industry to monitor pressure changes in various processes, including chemical processing and water treatment. These sensors help control the flow of materials in manufacturing processes and maintain optimal conditions for production.ConclusionSilicon pressure sensors are versatile and durable sensors that have a wide range of applications across various industries. They provide high accuracy, low power consumption, and are compact, making them ideal for use in numerous portable devices. As technology continues to evolve, the applications of silicon pressure sensors are expected to grow, making them a critical component of modern industries.
Ultrasonic Vs Pressure Water Level Measurement: Which Method is More Reliable?
article about the benefits of ultrasonic water level measurement over pressure-based measurement.Water Level Measurement: Ultrasonic vs. Pressure-basedAccurately measuring water levels is essential in a variety of applications, such as water treatment facilities, irrigation systems, and flood detection systems. Traditionally, water level measurement has been done using pressure-based sensors, which measure the water pressure at a certain depth. However, ultrasonic sensors are becoming increasingly popular due to their many benefits over pressure-based sensors.One major advantage of ultrasonic sensors is their accuracy. Unlike pressure-based sensors, which can be affected by changes in temperature, ultrasonic sensors measure the time it takes for sound waves to travel from the sensor to the water surface and back. This means that ultrasonic sensors can provide highly accurate measurements regardless of environmental fluctuations.Another benefit of ultrasonic sensors is their versatility. Ultrasonic sensors can be used in a wide range of applications, including open channels, tanks, and wells. They can also measure water levels with high accuracy over long distances, making them ideal for large bodies of water or difficult-to-reach areas.Ultrasonic sensors are also more reliable than pressure-based sensors. Pressure-based sensors are more prone to clogging, which can affect their accuracy. On the other hand, ultrasonic sensors usually only require periodic cleaning to maintain their accuracy.In addition, ultrasonic sensors are more cost-effective over the long term. Pressure-based sensors require regular calibration and maintenance, which can be costly. Ultrasonic sensors, on the other hand, have a longer lifespan and require less maintenance, making them a more cost-effective option in the long run.One company that offers ultrasonic water level measurement solutions is {}. With over {} years of experience in the industry, {} provides a range of ultrasonic sensors that are designed for various applications. Their sensors are highly accurate and reliable, making them ideal for a wide range of industries, including water management, agriculture, and environmental monitoring.In conclusion, ultrasonic sensors offer a range of benefits over pressure-based sensors for water level measurement. They offer greater accuracy, versatility, reliability, and cost-effectiveness, making them an increasingly popular choice for a wide range of applications. If you are in need of water level measurement solutions, consider exploring the benefits of ultrasonic technology and contacting {} for more information.