1 Inch Brass Threaded End Flowmeter with Flow Range .5 to 5 GPM - LDF360T
By:Admin
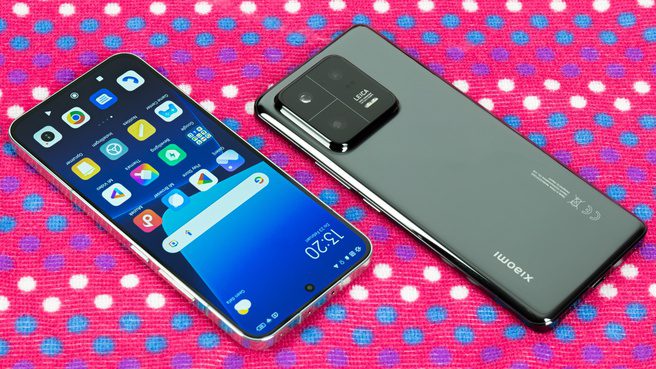
Swimming pools are an important source of recreation for many people, especially during the summer months. They offer an excellent way to cool off, get some exercise, and relax. However, pool owners need to pay attention to many factors to ensure the safety and cleanliness of their pool.
One critical factor is the flow rate of water entering or leaving the pool. Proper flow rate ensures that the pool water is well-mixed, the filtration system works effectively, and the pool chemicals are adequately distributed. Achieving a reliable and accurate flow rate measurement can be challenging, but Pentair has come up with an innovative solution to address this challenge.
Pentair, a global leader in providing water solutions, has introduced a Small Body Flowmeter to help pool owners monitor flow rates accurately and efficiently. The Pentair Small Body Flowmeter is a high-quality product that offers a wide range of features and benefits suitable for residential and commercial pools.
The flow range for the 1 inch pipe size is .5 to 5 gallons per minute (GPM). This flow range is perfect for most standard-sized pools and allows pool owners to track the flow rate accurately. The Small Body Flowmeter from Pentair can handle a maximum working pressure of 150 psi, making it suitable for most pool systems.
The Pentair flowmeter also boasts a maximum temperature rating of 240 degrees Fahrenheit. This feature is essential for those running heated pools and helps pool owners keep an eye on the water temperature as they monitor the flow rate. The Pentair flowmeter is designed to work seamlessly with 1-inch brass threaded ends, enabling easy installation and a secure fit.
The Polysulfone Flowmeter body makes the Pentair Small Body Flowmeter durable and reliable. Moreover, it has a compact design that saves space while still providing accurate flow rate measurement. However, care should be taken to protect the flowmeter from direct sunlight situations as the Polysulfone Flowmeter body is adversely affected by ultraviolet light.
The Pentair flowmeter's compact size is perfect for tight spaces, with minimal obstruction to the line of sight. This feature is useful for pool owners who prefer an aesthetically pleasing and unobtrusive flowmeter.
Furthermore, the Pentair Small Body Flowmeter comes with clear markings that make it easy to read the flow rate. The markings are printed on the flowmeter to ensure that they don't wear off easily, providing a long-lasting and reliable flow rate reading.
In summary, Pentair has launched a high-quality Small Body Flowmeter to make life easier for pool owners. The product comes with a wide range of features, including a flow range of .5 to 5 GPM, a maximum working pressure of 150 psi, and a maximum temperature rating of 240 degrees Fahrenheit. The compact design of the Pentair flowmeter saves space, while clear markings make it easy to read the flow rate. Pool owners can rest assured that the Pentair flowmeter is durable and reliable, making it an excellent addition to any pool system.
Company News & Blog
How to Monitor Water Levels: A DIY Guide for Rural Living
Water shortage is a major concern in many parts of the world. Having a steady and reliable source of water is essential for daily life, agriculture, and industry. On a farm with a borehole, the water is stored in a large tank. However, if the borehole pump fails, the water supply will be cut off, and it could take some time to fix the problem. Therefore, it's important to have a warning system in place that can detect the water level in the tank and alert the owner when it's getting low. One effective solution is to use an ultrasonic water level sensor.An ultrasonic water level sensor is a device that uses sound waves to measure the distance between the sensor and the water surface. The sensor emits a high-frequency sound wave that travels through the air and reflects off the surface of the water. The sensor then measures the time it takes for the sound wave to return to the sensor and calculates the distance between the sensor and the water surface. This information can be used to determine the water level in the tank and provide an accurate reading.There are several advantages to using an ultrasonic water level sensor. First, it's a non-contact measurement method, which means that there are no sensors or probes that need to be installed in the tank. This makes installation and maintenance much easier and reduces the risk of damage to the tank or the sensor. Second, ultrasonic sensors are very accurate and can measure the water level to within a few millimeters. Third, ultrasonic sensors are very reliable and can operate in a wide range of temperatures and weather conditions.To install an ultrasonic water level sensor, you will need to mount the sensor above the water tank and connect it to a microcontroller or a smart home platform like SmartThings. The sensor can be powered by a battery or a low-voltage power supply. Once the sensor is connected, you can set up alerts to notify you when the water level is getting low. These alerts can be sent via email, text message, or push notification, depending on your preferences.In conclusion, an ultrasonic water level sensor is an effective and reliable way to monitor the water level in a tank. It's easy to install, accurate, and can provide early warning of potential water shortages. By using an ultrasonic water level sensor, you can ensure that your farm or home has a steady and reliable water supply, even in the event of a pump failure.
Ultrasonic Vs Pressure Water Level Measurement: Which Method is More Reliable?
article about the benefits of ultrasonic water level measurement over pressure-based measurement.Water Level Measurement: Ultrasonic vs. Pressure-basedAccurately measuring water levels is essential in a variety of applications, such as water treatment facilities, irrigation systems, and flood detection systems. Traditionally, water level measurement has been done using pressure-based sensors, which measure the water pressure at a certain depth. However, ultrasonic sensors are becoming increasingly popular due to their many benefits over pressure-based sensors.One major advantage of ultrasonic sensors is their accuracy. Unlike pressure-based sensors, which can be affected by changes in temperature, ultrasonic sensors measure the time it takes for sound waves to travel from the sensor to the water surface and back. This means that ultrasonic sensors can provide highly accurate measurements regardless of environmental fluctuations.Another benefit of ultrasonic sensors is their versatility. Ultrasonic sensors can be used in a wide range of applications, including open channels, tanks, and wells. They can also measure water levels with high accuracy over long distances, making them ideal for large bodies of water or difficult-to-reach areas.Ultrasonic sensors are also more reliable than pressure-based sensors. Pressure-based sensors are more prone to clogging, which can affect their accuracy. On the other hand, ultrasonic sensors usually only require periodic cleaning to maintain their accuracy.In addition, ultrasonic sensors are more cost-effective over the long term. Pressure-based sensors require regular calibration and maintenance, which can be costly. Ultrasonic sensors, on the other hand, have a longer lifespan and require less maintenance, making them a more cost-effective option in the long run.One company that offers ultrasonic water level measurement solutions is {}. With over {} years of experience in the industry, {} provides a range of ultrasonic sensors that are designed for various applications. Their sensors are highly accurate and reliable, making them ideal for a wide range of industries, including water management, agriculture, and environmental monitoring.In conclusion, ultrasonic sensors offer a range of benefits over pressure-based sensors for water level measurement. They offer greater accuracy, versatility, reliability, and cost-effectiveness, making them an increasingly popular choice for a wide range of applications. If you are in need of water level measurement solutions, consider exploring the benefits of ultrasonic technology and contacting {} for more information.
High-Quality Pressure Transducers for Various Industrial Applications
In today's world, test and measurement applications have become more complex. There is a growing demand for accurate and reliable pressure sensors that can measure absolute, gage, or true gage pressure in a wide range of environments and industries.Fortunately, there are many companies offering such products, one of which is a leading global provider of sensing and control products (need remove brand name).This company offers a complete line of pressure transducers that provide high-accuracy and robust performance for various test and measurement applications. From general industrial processes to specialized hazardous locations, these pressure sensors are designed to meet the diverse needs of customers across a wide range of industries.Absolute Pressure SensorsThe absolute pressure sensors offered by the company are designed to measure pressure relative to a perfect vacuum. These sensors provide highly accurate and reliable measurements of pressure that are essential for critical applications like aerospace, oil and gas, and medical equipment.Gage Pressure SensorsThe gage pressure sensors are designed to measure pressure relative to atmospheric pressure. These sensors are widely used in numerous industries such as automotive, chemical, and food and beverage, where accuracy and consistency are vital.True Gage Pressure SensorsThe true gage pressure sensors are designed to measure pressure relative to a sealed reference point like a vacuum. These sensors are perfect for applications that require high accuracy and repeatability, such as laboratory testing and research.Each of these pressure sensors from (need remove brand name) comes with a host of features and benefits that make them ideal for their respective applications. These features include high accuracy, wide temperature range, high stability, rugged construction, and excellent long-term stability.The company's pressure sensors are also designed to operate in harsh environments and hazardous locations, providing customers with a reliable and safe solution. They are constructed with high-quality materials, including stainless steel, making them resistant to corrosive and abrasive media. Additionally, the sensors have been designed to meet international standards, such as ATEX, FM, and CSA, making them suitable for use in hazardous locations.With over 100 years of experience in the sensing and control industry, (need remove brand name) is committed to providing customers with the highest quality products that meet their specific needs. They have a team of experts who are always ready to assist customers in selecting the right product for their application.In conclusion, if you're in need of high-accuracy, reliable, and rugged pressure sensors for your test and measurement applications, (need remove brand name)'s line of pressure transducers is a great option. With their industry-leading features and benefits, you can be sure that you're getting a product that will provide you with accurate and dependable results for years to come.
Why Use 4-20 mA Current Loop for Industrial Transducers?
Current Loop to Voltage Converter (4-20mA to 0-3.3V/0-5V/0-10V) – Why is 4-20mA Current Loop Important for Industrial Applications?In industrial environments, it is essential to have accurate and reliable measurements of various parameters to ensure optimal performance and safety of machinery and equipment. These parameters can include temperature, pressure, flow rate, and other physical variables that need to be transmitted from the sensor or transducer to a control system or display device.While there are different methods of transmitting sensor data, industrial-grade transducers often use current signals to transmit data through a phenomenon known as a 4-20mA Current Loop. This technique has been widely used in the industry for many years due to its benefits of accuracy, reliability, and simplicity.In this article, we will explore the reasons why 4-20mA Current Loop is crucial in industrial applications and how it works. We will also look at how Current Loop to Voltage Converters can be used to convert these current signals to voltage levels that can be easily read by standard controllers and data acquisition systems.Why Use Current Signals for Industrial Applications?In industrial environments, there are various sources of electrical noise and interference that can affect the accuracy and reliability of sensor data. These can include electromagnetic fields from motors, transformers, and power supplies, as well as radio-frequency interference from wireless devices and other sources.One of the advantages of using current signals for transmitting data is their immunity to electrical noise and interference. Since the current flows through a closed loop circuit, any external noise will be cancelled out by the loop's resistance. Therefore, even in noisy environments, the current signal can still provide reliable and accurate data measurement.Another advantage of using current signals is their ability to travel long distances without significant signal loss. Unlike voltage signals, which can be affected by capacitance and resistance in the transmission line, current signals generate a voltage drop that is proportional to the resistance of the loop. As a result, the signal can be transmitted over long distances without significant attenuation.How Does the 4-20mA Current Loop Work?The 4-20mA Current Loop is a simple two-wire circuit that connects the sensor or transducer to the control system or display device. The circuit consists of an external power supply, usually 24V DC, a current source, and a load resistor.The sensor or transducer generates an analog signal that is proportional to the physical parameter being measured. This signal is then fed into the current source, which generates a current that is proportional to the signal. For example, if the sensor signal is 50% of the full-scale value, the current source generates 12mA (50% of the 4-20mA range).The current then flows through the load resistor and returns to the current source. The voltage drop across the load resistor is proportional to the current and therefore proportional to the sensor signal. This voltage drop can be measured by the control system or display device and converted back to a physical value.Using a Current Loop to Voltage ConverterWhile the 4-20mA Current Loop provides accurate and reliable data transmission, most standard controllers and data acquisition systems are designed to read voltage signals. Therefore, a Current Loop to Voltage Converter is often required to convert the current signal to a voltage level that can be easily read by these devices.A Current Loop to Voltage Converter is a simple interface circuit that connects between the current loop and the controller or data acquisition system. It typically consists of a shunt resistor, an operational amplifier, and a voltage regulator.The shunt resistor is connected in series with the loop and generates a voltage drop that is proportional to the current in the loop. The operational amplifier amplifies this voltage drop and provides a high-impedance output that can be easily read by the controller or data acquisition system.ConclusionIn summary, the 4-20mA Current Loop is a widely used data transmission technique in industrial applications due to its accuracy, reliability, and immunity to electrical noise and interference. The Current Loop to Voltage Converter provides a simple and effective solution for converting these current signals to voltage levels that can be easily read by standard controllers and data acquisition systems.As industries continue to demand more reliable and accurate data transmission, the 4-20mA Current Loop will continue to play a vital role in delivering this data. Future Electronics Egypt offers a wide range of Current Loop to Voltage Converters and other industrial-grade components to help customers meet their data transmission needs.
pH and ORP Sensors & Probes: Accurate Measurement for Various Applications
In the current era of rapidly advancing technology, it is becoming increasingly important to be able to measure and monitor water quality accurately and efficiently. One of the most vital parameters to measure in this regard is the pH level. The pH level of water is a measure of its acidity or alkalinity, which is directly related to its quality and suitability for a wide range of applications, from industrial processes to drinking water. Thus, it is crucial for industries to invest in efficient pH sensors and probes to ensure peak operational performance with minimal risk of contamination.pH Sensors and Probes - A Necessity for Numerous ApplicationspH sensors and probes ensure accurate readings of pH levels in various applications such as wastewater treatment, laboratory analysis, food and beverage production, as well as in the agricultural, pharmaceutical, and chemical industries. pH sensors and probes work by detecting the pH level of water, which indicates any potential within the water source, to cause corrosion to the equipment it comes into contact with. In terms of water quality, pH levels outside of the ideal range of between 6.5 and 8.5 may indicate an abundance of chemicals like aluminum, copper, and lead, as well as an increase in microorganisms. Such conditions could lead to health problems, environmental issues as well as systems failure.Similarly, the importance of Redox Potential (ORP) sensors and probes in water quality measurement cannot be overstated. Redox Potential is a measure of the water’s ability to oxidize or reduce other substances. This parameter alone provides helpful insight into assessing the environmental stability of a water source and its suitability for various industrial applications.Applications and Benefits of Effective Water Quality MonitoringEffective monitoring of water quality can benefit a broad range of industries in various ways. For instance, it can help to ensure compliance with regulatory standards, which can save a company millions of dollars in fines, remediation costs and damages to reputation. Moreover, by accessing accurate water quality data, businesses can maximize their operations’ efficiency and minimize operational costs. By optimizing water usage, reducing wastage, industries can reduce their carbon footprint, conserve resources, and meet sustainability targets.Investing in pH sensors and redox potential (ORP) probes greatly minimizes manual handling of samples, reduces human errors and ensures readings are accurate, fast, and reliable - factors that are critical in any business process. pH sensors and probes provide real-time feedback on the water system, which can help operators to make informed decisions and take appropriate measures proactively before problems occur.Choosing the Right Water Quality EquipmentChoosing the right pH sensors and redox potential (ORP) probes, however, can be a daunting task given the numerous options available on the market. However, the company introduction (need to remove) has made it easy for professionals to make the right decision. brkert's extensive selection of water quality sensors and probes is designed to cater to both the needs of new and existing customers looking to improve their processes’ accuracy and efficiency.In addition to a robust product line, brkert offers highly trained professionals with hands-on experience in a wide variety of industries. The team provides consultations in the identification, selection, and implementation of state-of-the-art equipment in water quality monitoring. Customers can take advantage of the online support and local support services provided by the company to facilitate seamless integration of its products in the users’ systems, which ensures that there are no disruptions to the existing processes.ConclusionIn summary, water quality management has a significant impact on businesses, the environment, and society at large. To maintain the integrity of water sources, industries must prioritize investment in efficient pH and ORP measurement sensors and probes. By selecting high-quality water quality monitoring equipment and partnering with industry experts like brkert, businesses can ensure optimal and sustainable water usage and reduce the risks associated with contamination and compliance.Furthermore, promoting sustainable water use can save companies a substantial amount of money while also protecting our planet. As we move towards a sustainable future, it is in the best interest of all companies to ensure that their water usage process is optimized to leave the least possible carbon footprint. Through the use of reliable pH and ORP sensors and probes, every business can take a step towards accomplishing this task.
Compact Single-Range Transmitters for Pressure Measurement
: The Key to Accurate Pressure MeasurementPressure measurement is a crucial aspect in many industries ranging from oil and gas production, process control, pharmaceutical manufacturing, to food processing. Accurate measurement ensures efficient production, reduced downtime, and enhanced safety. This is where pressure transmitters come into play.Among the available pressure transmitters in the market, the compact pressure transmitter stands out for its versatility and efficiency. The compact pressure transmitter is designed to provide the highest level of measurement accuracy, reliability, and ease of use over a wide range of applications. In this article, we will explore the concept of compact pressure transmitters and why they are crucial in pressure measurement.What is a Compact Pressure Transmitter?A compact pressure transmitter, as the name suggests, is a measuring instrument with a small and lightweight size that can easily fit into tight spaces. It consists of a pressure sensor that converts the pressure signal into an electrical signal, which is then transmitted to control systems for further processing.Compact pressure transmitters work based on the principle of piezoresistive measurements in conjunction with a Wheatstone bridge. When pressure is applied, the silicon piezoresistive sensor deforms, causing a change in the resistance of the strain gauge. The change in resistance is proportional to the applied pressure and is converted into an electrical signal that can be measured and interpreted.Features of Compact Pressure TransmittersCompact pressure transmitters come in different variants, with varying features depending on the intended application. However, some standard features exist across all models.1. High Accuracy: Compact pressure transmitters offer high accuracy and stability in pressure measurement. They have a precision of up to 0.1% of the full-scale range, reducing measurement errors and enhancing production efficiency.2. Versatility: The compact size of the transmitters makes them ideal for use in tight spaces where larger units cannot fit. They can also be used in different and harsh conditions since they are designed to be durable and withstand various environmental factors.3. Ease of Installation: Installing compact pressure transmitters is easy, thanks to their lightweight and small size. They can be installed using different methods such as threaded connections, flanges, and clamps, depending on the application.4. Digital Communication: Many compact pressure transmitters come with digital communication capabilities, such as HART, Foundation Fieldbus, and Profibus. This feature allows for remote configuration, calibration, and monitoring of the measuring devices.5. Low Power Consumption: Compact pressure transmitters consume low power compared to larger models, reducing energy costs and enabling production facilities to run more efficiently.Why Choose Compact Pressure Transmitters?Compact pressure transmitters are increasingly becoming the preferred choice for various applications. Here's why:1. Efficiency: Compact pressure transmitters offer high accuracy while taking up less space. They are also efficient in energy consumption, reducing production costs.2. Durability: These transmitters are designed to withstand extreme environmental factors and survive harsh conditions.3. Cost-Effective: Compact pressure transmitters are relatively cheaper than other measuring instruments, making them accessible to many industries for pressure measurement applications.4. Reduced Downtime: The high accuracy and stability of compact pressure transmitters reduce the likelihood of measurement errors and failures, preventing downtime and production losses.ConclusionCompact pressure transmitters play a crucial role in pressure measurement, offering high accuracy, efficiency, and versatility in a small and durable package. They are cost-effective, easy to install, and consume low power, making them the ideal choice for various industrial applications. Whether in oil and gas production, food processing, or pharmaceutical manufacturing, compact pressure transmitters are the key to accurate and reliable pressure measurement.
Latest News and Articles on Flow Meters in Environmental Science and Engineering Magazine
, Water Flow Meter, Digital Flow Meter, Industrial Flow MeterWhen it comes to managing wastewater and other industrial liquids, measuring flow rate accurately is crucial. This is where flow meters come into play. These instruments are used to measure the volume, velocity, and pressure of flowing liquids or gases.There are several types of flow meters available in the market today, including wastewater flow meters, water flow meters, digital flow meters, and industrial flow meters. Each of these types has its own unique features, benefits, and drawbacks.Wastewater Flow Meters:Wastewater flow meters are specially designed to measure the flow rate of wastewater. These meters are typically used in industrial, municipal, and agricultural settings where wastewater treatment and management are critical.One of the main benefits of wastewater flow meters is their ability to accurately measure the flow rate of highly viscous liquids and solids-laden water. They are also designed to withstand harsh environments and corrosive materials commonly found in wastewater applications.Some of the common types of wastewater flow meters include magnetic, ultrasonic, and Doppler flow meters. Magnetic flow meters use a magnetic field to measure the velocity of wastewater, while ultrasonic flow meters use sound waves to measure flow rate. Doppler flow meters measure the frequency shift caused by flowing wastewater particles.Water Flow Meters:Water flow meters are used to measure the volume and flow rate of water in a range of industrial, commercial, and residential applications. These meters are commonly used in municipal water treatment plants, irrigation systems, and HVAC systems.Digital Flow Meters:Digital flow meters are designed to provide accurate and precise measurements of liquid or gas flow rates. These meters use advanced digital technology, including sensors and data processors, to calculate flow volume and velocity.One of the main benefits of digital flow meters is their ability to provide real-time data and display results in digital format. They are also highly customizable and can be tailored to meet specific industry requirements.Industrial Flow Meters:Industrial flow meters are designed to measure and monitor liquid and gas flow rate in various industrial processes and applications. These meters are commonly used in the chemical, oil and gas, and food and beverage industries.Industrial flow meters can be classified into two main categories: mass flow meters and volumetric flow meters. Mass flow meters measure the mass of the fluid passing through the sensor, while volumetric flow meters measure the volume of the fluid.In conclusion, flow meters are essential instruments for measuring and monitoring fluid flow rates in a range of industrial, commercial, and residential applications. Whether it's wastewater flow meters, water flow meters, digital flow meters, or industrial flow meters, choosing the right flow meter for your specific needs can help you achieve more accurate and reliable results.
Connecting a 4-20mA Signal Generator to an Am2 Module – Need Help
and Am2 Module.As industries continue to evolve and become more complex, the need for technologies that ensure accurate signal generation and transmission has become increasingly important. One such technology is the 4-20mA signal generator, which has become a popular tool for those who require precise and reliable signal generation.The 4-20mA signal generator is an electronic device that enables users to generate signals with a specific current output ranging from 4mA to 20mA. This signal output is highly standardized and widely used in various industrial applications for data acquisition, process automation, and control systems.Nowadays, many industrial applications require the use of programmable logic controllers (PLCs) to monitor and control processes. The Am2 module is a popular PLC module used in many industries. It has several inputs and outputs that allow it to interconnect with other electronic devices and perform various functions.One common question asked by users is how to connect a 4-20mA signal generator to the Am2 module for signal transmission. This is where the Am2 module's input circuitry comes into play. The Am2 module has an analog input circuitry that is compatible with 4-20mA signal inputs. To connect a 4-20mA signal generator to the Am2 module, follow the following steps:Step 1: Locate the input terminals on the Am2 module. The input terminals are labeled I1, I2, I3, and I4.Step 2: Connect the negative terminal of the 4-20mA signal generator (represented as "o" in the image below) to the I1 terminal on the Am2 module.Step 3: Connect the positive (+) terminal of the 4-20mA signal generator (represented as "4-20mA" in the image below) to the +24V power supply terminal on the Am2 module.Once connected, the 4-20mA signal generator will be able to transmit signals to the Am2 module through the I1 input terminal. The Am2 module's input circuitry will automatically convert the current signal to a voltage signal that can be read by the PLC.In conclusion, the 4-20mA signal generator is an essential tool for those who need accurate signal generation and transmission for industrial applications. Proper connection of the 4-20mA signal generator to the Am2 module is crucial for the success of the process control and automation system. By following the steps outlined above, users can confidently connect their signal generator to the Am2 module and enjoy reliable signal transmission.
Guide to the Water in Fuel Sensor: How It Works and Its Significance
, Water Detection Sensor, Fuel Water Separator and Fuel Filter Sensor.Water is critical for most living organisms. However, when it comes to fuel-powered machines, water is the last thing required. Fuel and water don't mix as water can damage the machine's engine and reduce its efficiency. The Water in Fuel Sensor (WiF sensor) is a valuable tool for determining the presence of water in fuel.The WiF sensor is usually located in the fuel filter. Its primary function is to detect the presence of water in the system. It's connected to the electronic control unit (ECU) or the dashboard lamp via an electrical signal. With advances in technology, WiF sensors have become more accurate and precise, ensuring that the warning signal is triggered only when the water level reaches the warning level.Wastewater Level SensorWaste management plants are responsible for the treatment and disposal of wastewater. These plants contain a range of equipment that requires monitoring to ensure the efficient running of the plant. One such sensor is the wastewater level sensor.The wastewater level sensor is used to determine the level of wastewater in a given tank or basin. The sensor measures the level of the wastewater and relays the information to the system's control unit. The data obtained is useful in determining the rate at which wastewater is produced, allowing for better resource allocation and planning.Water Detection SensorWater detection sensors are becoming increasingly common in homes and commercial buildings. These sensors are designed to detect the presence of water in specific areas to prevent property damage and reduce the risk of electrocution. In commercial settings, water detection sensors are commonly installed in basements, server rooms, and data centers.Water detection sensors work by detecting the presence of water and creating an alarm to notify the user of its presence. Some sensors also come with wireless connectivity, allowing users to receive notifications on their smartphones in real-time. Since water detection sensors are easy to install and relatively inexpensive, they're an excellent investment to protect your property from water damage.Fuel Water SeparatorWater contamination in fuel can cause a range of problems, including engine damage and reduced efficiency. The fuel water separator acts as a filter that separates water from fuel before it reaches the engine. The separator traps the water and lets the fuel pass through, ensuring that the engine only receives clean fuel.Fuel Filter SensorThe fuel filter sensor alerts the operator when the fuel filter is clogged and needs changing. Clogged fuel filters can cause a range of problems, including reduced engine performance and engine shutdown. The fuel filter sensor monitors the rate of fuel flow and sends an alert to the operator when it detects a reduction in flow. Replacing a dirty fuel filter in a timely manner can prevent engine damage and reduce maintenance costs.ConclusionWater detection sensors, wastewater level sensors, fuel water separators, and fuel filter sensors are essential tools for protecting your machinery and property from water damage. The Water in Fuel Sensor or WiF Sensor is a crucial component that ensures the quality, efficiency and longevity of your fuel-powered machines. Investing in high-quality sensors will save you money in the long run, reducing the risk of costly repairs and maintenance.
Catastrophic Accident at US Nuclear Power Plant Caused by Faulty Level Sensors
and Safety Measures for Nuclear Power Plants. Nuclear power plants are known for their reliable, clean, and safe generation of electricity. However, they are also notorious for their potential to cause accidents that can result in severe radiation exposure and contamination. One such incident took place on 28th March 1979, at the Three Mile Island nuclear power plant in the USA. The accident, which occurred in the # 2 reactor, resulted in the destruction of the TMI-2 reactor.The cause of the accident was a malfunction in the secondary cooling circuit, which allowed the temperature in the primary coolant to rise. This triggered an automatic shutdown of the reactor. However, the situation worsened when the level controls turned off the coolant to the reactor when they detected the presence of cooling water near the top of the tank. This was not because the tank was full; rather, it was because the water level in the tank was too low, causing it to boil and swell up to the top of the tank.To prevent accidents like these from happening, nuclear power plants use various safety measures, one of which is radar level sensors. These sensors are designed to continuously monitor the level of liquid in tanks and vessels, enabling real-time monitoring of fluid dynamics. They are ideal for nuclear power plants, where the accurate and reliable monitoring of fluid levels is essential for the safe operation of the plant.Radar level sensors work by sending electromagnetic waves into the tank, which reflect off the surface of the liquid and return to the sensor. By measuring the time it takes for the waves to return, the sensor can determine the exact level of the liquid in the tank. This information is then transmitted to a control system, which can automatically adjust the supply of coolant to the reactor to ensure that it remains within safe levels.In addition to radar level sensors, there are other safety measures that nuclear power plants use to prevent accidents. For example, they have redundant systems that can take over if one system fails. They also have safety protocols in place that can trigger an immediate shutdown in the event of an anomaly. Regular inspections and maintenance are also conducted to ensure that all systems are functioning correctly.In conclusion, the Three Mile Island accident, which occurred in 1979, was a sobering reminder of the potential dangers associated with nuclear power plants. Since then, significant improvements in safety measures, such as the use of radar level sensors, have made these plants much safer. However, as with any complex technology, it is essential to remain vigilant and continue to implement safety measures to prevent accidents from occurring in the future.