New Level Transmitter Technology Eliminates Impulse Lines and Capillary Tubes
By:Admin
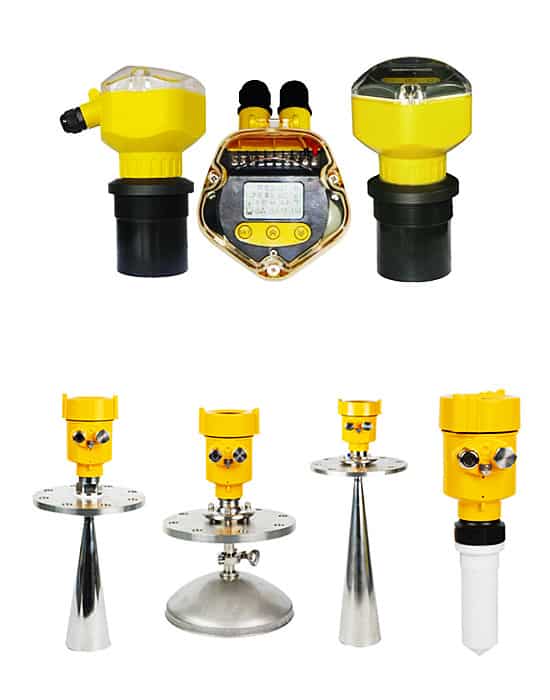
In traditional DP level transmitters, impulse lines and capillary tubes were used to transmit the pressure difference between the liquid and the reference pressure to the measuring cell. However, these lines and tubes were prone to clogging, leakage, or freezing, which caused inaccurate measurements and increased maintenance costs.
Thanks to technological advancements, DP level transmitters have evolved to overcome the limitations of traditional designs. Modern DP level transmitters do not use impulse lines or capillary tubes, making them easier to install, operate, and maintain. Instead, they use electronic remote seals or direct-mount seals, which eliminate the need for long tubing runs.
Electronic remote seals use a digital signal processor (DSP) to convert the pressure signals from the remote seal into a standard output signal. The remote seal can be located up to 328 feet away from the transmitter, allowing it to be installed in harsh or hazardous environments. The signal is transmitted via two-wire technology, eliminating the need for additional wiring and reducing installation costs.
Direct-mount seals can be mounted directly on the process connection of the transmitter, eliminating the need for impulse lines or capillary tubes. They are available in a range of materials and designs to meet different process requirements. Direct-mount seals are easy to install, and they do not require additional calibration or adjustment.
Capillary level transmitters offer an alternative solution that eliminates the need for impulse lines and capillary tubes. Instead, they use a single capillary tube to connect the process connection to the measuring cell. The capillary tube is filled with a special fluid that transmits the pressure difference to the cell. Capillary level transmitters are accurate and reliable, and they offer excellent stability over a wide range of process temperatures and pressures.
In conclusion, DP level transmitters have come a long way since the traditional designs that used impulse lines and capillary tubes. Modern transmitters offer several solutions that eliminate the need for these lines, making them more reliable, accurate, and easy to maintain. Capillary level transmitters offer additional advantages that make them ideal for certain process applications. When selecting a DP level transmitter, it’s important to consider the specific requirements of the process and choose the best solution that meets those needs.
Company News & Blog
Premium Selection of Ultrasonic Flowmeters and Water Flowmeters with Customer Reviews and Detailed Product Information
and Water Flow Meter Supplier.Ultrasonic Flow Meters and Water Flow Meters: An OverviewFluid measurement is an important aspect of many modern industries, such as engineering, manufacturing, and environmental monitoring. Accurate flow measurement of liquids and gases is crucial for making informed decisions and managing processes effectively. Ultrasonic Flow Meters and Water Flow Meters are two types of equipment commonly utilized for measuring fluid flow.Ultrasonic Flow MetersUltrasonic Flow Meters use ultrasonic waves to measure the velocity of liquid or gas flow within a pipe. The technology involves emitting high-frequency sound waves from a transmitter to a receiver unit. As the sound waves travel through the fluid, they will experience a shift in frequency due to the relative velocity of the fluid against the transmitter and receiver. This frequency shift allows the Ultrasonic Flow Meter to calculate the velocity of the fluid.Ultrasonic Flow Meters come in two main types: Transit-time and Doppler. Transit-time uses two ultrasonic transmitters and receivers to measure the time it takes for ultrasonic signals to travel upstream and downstream against the flow. Doppler, meanwhile, uses a single transducer to send ultrasonic signals at an angle to the flow to measure the reflection of sound waves against particles or bubbles within the fluid.Ultrasonic Flow Meters have significant advantages over traditional devices, such as mechanical flow meters, as they do not impede flow or require internal parts to make direct contact with the fluid. Additionally, Ultrasonic Flow Meters are accurate, non-invasive, and do not wear out or require maintenance frequently.Water Flow MetersWater Flow Meters, as their name suggests, are used specifically for measuring water flow. They function by measuring the amount of water passing through a pipe over a given time. Water Flow Meters come in various types, but the most commonly used are mechanical and electronic meters.Mechanical meters use a wheel or vane to react to the water flow and measure the volume of water passing through the meter. Electronic meters, on the other hand, use magnetic or ultrasonic sensors to detect water flow, convert this into an electrical signal, and display the volume on an electronic display.Water Flow Meters are useful for monitoring water usage in industrial, commercial, and residential settings. They can also be used to detect leaks, analyze water usage patterns, and ensure compliance with water usage regulations.Ultrasonic Level Meter Supplier and Water Flow Meter SupplierIn conclusion, Ultrasonic Flow Meters and Water Flow Meters are essential tools for fluid measurement in various industries. They provide reliable, accurate, and non-invasive means of monitoring fluid flow and detecting any anomalies promptly.For those in need of Ultrasonic Level Meter Supplier or Water Flow Meter Supplier, it is crucial to choose a reputable supplier that can provide high-quality products, reliable customer support, and competitive pricing. It is always recommended to read genuine customer reviews and conduct thorough research before making any purchase decisions.When choosing a supplier, it is essential to consider the supplier's experience in the industry, the quality of their products and services, and their reputation within the market. Additionally, choosing a supplier that provides additional services such as calibration and maintenance can help ensure the longevity and accuracy of the flow meters.In summary, Ultrasonic Flow Meters and Water Flow Meters are indispensable tools for fluid measurement and management. Choosing a reliable supplier is essential, and it will ensure that the equipment performs accurately and efficiently for many years to come.
Shop Quality Level Measuring Instruments from Top Suppliers in China - Available Now at Discounted Prices!
Level measuring instruments are an essential tool that is used across many industries. They are primarily used to determine the level of liquids or powder-like materials in tanks and silos. The use of these instruments enables manufacturers to keep track of inventory levels, improve production processes, and prevent overflows. There are different types of level measuring instruments, with one of the most popular being radar level instruments.Radar level instruments use radar waves to determine the level of liquids or materials in tanks. They offer many advantages, including accuracy, reliability, and versatility. They are particularly useful in applications where there are materials that are difficult to measure or where there are harsh conditions, such as high temperatures, pressure, and humidity.One of the key advantages of radar level instruments is their accuracy. They provide precise measurements, even in the presence of obstacles, such as nozzles or agitators. Their accuracy is also not affected by changes in the liquid or material properties, such as density or viscosity. Additionally, they can measure levels that are as low as a few millimeters or as high as several meters.Another advantage of radar level instruments is their reliability. Unlike other types of level measuring instruments, such as ultrasonic or capacitive sensors, radar instruments do not require contact with the material being measured. This means that there is no wear and tear on the sensor, reducing the need for maintenance. Additionally, radar instruments are not affected by changes in the environment, such as temperature or humidity.Radar level instruments are also highly versatile. They can be used to measure a wide range of liquid or material types, including corrosive and abrasive substances. Additionally, they can be used in many different applications, from food production to chemical processing. Because they are non-contact and do not require calibration, they are also easy to install and integrate into existing systems.In conclusion, radar level instruments are an important tool for many industries. Their accuracy, reliability, and versatility make them an ideal choice for measuring liquid or material levels in tanks and silos. They are particularly useful in applications where materials are difficult to measure or where there are harsh conditions. If you are in the market for a level measuring instrument, be sure to consider a radar level instrument for its many advantages and benefits.
Hydrostatic Level Probe for Wastewater - Piezoresistive and Differential Pressure Options
A hydrostatic level probe is an essential instrument used to measure the level of liquids, particularly wastewater. It is an innovative solution that provides accurate measurements in submerged environments and helps monitor the liquid levels in tanks and vessels.The hydrostatic level probe works on the basis of hydrostatic pressure principles. It measures the pressure exerted by the liquid on the bottom of the tank. This pressure reading is then transformed into a level measurement that helps operators optimize their wastewater treatment systems.There are several types of hydrostatic level probes available in the market, including piezoresistive, differential pressure, and submersible level sensors. They vary in terms of their technology, construction, measurement range, and accuracy. One of the most popular options is the Piezo As Hydrostatic Level Probe.The Piezo As Hydrostatic Level Probe is an advanced and reliable liquid level measuring instrument that uses piezoresistive technology for accurate measurements in challenging industrial environments. The probe consists of a high-precision ceramic measuring cell with fully integrated electronics that deliver reliable and accurate results.The probe is designed to withstand harsh conditions, including corrosive and abrasive substances, and can operate at high temperatures and pressures. It is suitable for use in various applications, such as water and wastewater treatment, chemical processing, and oil and gas refining.With a measurement range of up to 1,000 meters and an accuracy of up to 0.1 percent, the Piezo As Hydrostatic Level Probe is an ideal choice for industrial liquid level measurement applications. The probe is easy to install, maintain, and integrate into existing control systems, and it provides reliable and accurate measurements even in challenging environments.In conclusion, wastewater treatment is critical to the environment and human health, and accurate level measurement is essential to optimize the process. The hydrostatic level probe, such as the Piezo As Hydrostatic Level Probe, is an efficient, cost-effective, and reliable solution that can deliver accurate measurements and help operators ensure the smooth operation of their wastewater treatment systems.
Why Use 4-20 mA Current Loop for Industrial Transducers?
Current Loop to Voltage Converter (4-20mA to 0-3.3V/0-5V/0-10V) – Why is 4-20mA Current Loop Important for Industrial Applications?In industrial environments, it is essential to have accurate and reliable measurements of various parameters to ensure optimal performance and safety of machinery and equipment. These parameters can include temperature, pressure, flow rate, and other physical variables that need to be transmitted from the sensor or transducer to a control system or display device.While there are different methods of transmitting sensor data, industrial-grade transducers often use current signals to transmit data through a phenomenon known as a 4-20mA Current Loop. This technique has been widely used in the industry for many years due to its benefits of accuracy, reliability, and simplicity.In this article, we will explore the reasons why 4-20mA Current Loop is crucial in industrial applications and how it works. We will also look at how Current Loop to Voltage Converters can be used to convert these current signals to voltage levels that can be easily read by standard controllers and data acquisition systems.Why Use Current Signals for Industrial Applications?In industrial environments, there are various sources of electrical noise and interference that can affect the accuracy and reliability of sensor data. These can include electromagnetic fields from motors, transformers, and power supplies, as well as radio-frequency interference from wireless devices and other sources.One of the advantages of using current signals for transmitting data is their immunity to electrical noise and interference. Since the current flows through a closed loop circuit, any external noise will be cancelled out by the loop's resistance. Therefore, even in noisy environments, the current signal can still provide reliable and accurate data measurement.Another advantage of using current signals is their ability to travel long distances without significant signal loss. Unlike voltage signals, which can be affected by capacitance and resistance in the transmission line, current signals generate a voltage drop that is proportional to the resistance of the loop. As a result, the signal can be transmitted over long distances without significant attenuation.How Does the 4-20mA Current Loop Work?The 4-20mA Current Loop is a simple two-wire circuit that connects the sensor or transducer to the control system or display device. The circuit consists of an external power supply, usually 24V DC, a current source, and a load resistor.The sensor or transducer generates an analog signal that is proportional to the physical parameter being measured. This signal is then fed into the current source, which generates a current that is proportional to the signal. For example, if the sensor signal is 50% of the full-scale value, the current source generates 12mA (50% of the 4-20mA range).The current then flows through the load resistor and returns to the current source. The voltage drop across the load resistor is proportional to the current and therefore proportional to the sensor signal. This voltage drop can be measured by the control system or display device and converted back to a physical value.Using a Current Loop to Voltage ConverterWhile the 4-20mA Current Loop provides accurate and reliable data transmission, most standard controllers and data acquisition systems are designed to read voltage signals. Therefore, a Current Loop to Voltage Converter is often required to convert the current signal to a voltage level that can be easily read by these devices.A Current Loop to Voltage Converter is a simple interface circuit that connects between the current loop and the controller or data acquisition system. It typically consists of a shunt resistor, an operational amplifier, and a voltage regulator.The shunt resistor is connected in series with the loop and generates a voltage drop that is proportional to the current in the loop. The operational amplifier amplifies this voltage drop and provides a high-impedance output that can be easily read by the controller or data acquisition system.ConclusionIn summary, the 4-20mA Current Loop is a widely used data transmission technique in industrial applications due to its accuracy, reliability, and immunity to electrical noise and interference. The Current Loop to Voltage Converter provides a simple and effective solution for converting these current signals to voltage levels that can be easily read by standard controllers and data acquisition systems.As industries continue to demand more reliable and accurate data transmission, the 4-20mA Current Loop will continue to play a vital role in delivering this data. Future Electronics Egypt offers a wide range of Current Loop to Voltage Converters and other industrial-grade components to help customers meet their data transmission needs.
Find Top Vortex Flow Meter Suppliers and Manufacturers on IQS Directory
and Suppliers, Vortex Flowmeter, Flowmeter Technology, High-Performance Products, Advanced Vortex Flowmeter Technology, and Quick Delivery.Vortex flowmeters are rapidly becoming the preferred choice of flow measurement devices for a wide range of applications. The ability to accurately measure flow while remaining practically immune to processing conditions such as temperature, pressure, viscosity, and flow rate makes vortex flowmeters quite attractive for use across several industries. When it comes to vortex flowmeters, one can choose from a list of leading manufacturers and suppliers with IQS Directory.At IQS Directory, you can save time by selecting from a list of leading vortex flowmeter manufacturers and suppliers offering advanced technology, quick delivery, and low pricing on high-performance products. With an extensive range of vortex flowmeter varieties to choose from, businesses can enjoy a hassle-free experience while selecting the perfect vortex flow meter for their application.As technology continuously advances, so do vortex flowmeters. Vortex flowmeters have been enhanced with advanced technology that helps to provide more accurate and reliable flow measurement data while offering improved performance. These advanced vortex flowmeters use state-of-the-art techniques that allow for the measurement of flow rate, pressure, and temperature, enabling companies to make better-informed decisions.Moreover, selecting a vortex flowmeter that is well-designed, easy to install, and features durable construction can ultimately lead to long-term reliability. Manufacturers and suppliers typically offer solutions that have been tested against harsh working conditions, ensuring that they deliver maximum return on investment while remaining operational and effective for a prolonged time.In terms of the delivery process, IQS Directory's list of vortex flowmeter manufacturers and suppliers offers quick shipping and dedicated customer support. With zero lead-time, businesses can get the flowmeter they need without having to wait for long periods, leading to an increase in productivity and fewer downtimes.In conclusion, when seeking to purchase vortex flowmeters, businesses can save time and resources by selecting from IQS Directory's list of leading vortex flowmeter manufacturers and suppliers. With advanced technology, quick delivery, and low pricing on high-performance products, businesses can enjoy the smoothest experience while selecting the perfect vortex flowmeter to meet their requirements. Advanced vortex flowmeter technology is making it increasingly possible to measure flow rate, pressure, and temperature with incredible accuracy and reliability. As a result, businesses can confidently make informed decisions that lead to better operational efficiency, increased productivity, and a stronger bottom line.
Effective Water Flow Measurement with Clamp-On Ultrasonic Flow Meter
article on the importance of water flow sensors in various industries.Water Flow Sensor: The Importance of Measuring Water Flow RatesWater is an essential resource in our daily lives and in various industries. Maintaining a consistent water flow rate and accurately measuring it is crucial for a variety of processes. That is where water flow sensors come into play. These devices are designed to measure the rate and quantity of water flowing through pipes and channels. They are used in a range of industries, including manufacturing, agriculture, environmental monitoring, and more.Industries that require water for their processes rely heavily on water flow sensors. For instance, the food and beverage industry needs to maintain a constant flow rate of water for cleaning and sterilization purposes. Any deviation in water flow rate can lead to contamination and affect product quality. In the pharmaceutical sector, water is a critical component in drug manufacturing, and any fluctuation in water flow rates can impact the final product's quality and efficacy.Water flow sensors are also widely used in irrigation systems, particularly in agricultural practices. These sensors help farmers to monitor the water flow rate and ensure that crops are receiving the required amount of water. Overwatering can lead to wastage of water and increase operational costs, while underwatering can cause crop failure and financial losses. Water flow sensors provide precise data, enabling farmers to make informed decisions about water usage and management.The mining and construction industry also relies on water flow sensors. In mining, water is used for dust suppression and mineral processing. In construction, water flow sensors are used for concrete mixing and dust suppression. Accurately measuring the water flow rate is essential in reducing water wastage, minimizing environmental impact, and reducing operational costs.Water flow sensors are also used in environmental monitoring. They are essential in measuring river and stream flow rates, which is critical in predicting flooding risks and managing water resource allocation. Additionally, they are used in wastewater treatment plants to measure the flow rate and adjust the treatment process accordingly. This helps in ensuring that only quality water is discharged back into the environment.In recent years, the use of water flow sensors has increased, thanks to technological advancements. One of the latest developments is the clamp-on ultrasonic flow meter. This type of flow meter is non-intrusive and can be quickly installed without disrupting operations. It uses ultrasonic sound waves to measure the velocity of water flow, which is then converted into a volumetric flow rate. The clamp-on design allows for easy installation and maintenance, eliminating the need for cutting pipes or introducing any foreign materials into the water flow.In Indonesia, Wiratama Mitra Abadi is one of the leading distributors of water flow sensors, including clamp-on ultrasonic flow meters. The company has been providing high-quality instrumentation, mechanical, and automation tools since 2004. They offer a wide range of water flow sensors from various manufacturers, providing clients with a variety of options to meet their unique needs.In conclusion, water flow sensors play a crucial role in various industries and processes. They help to ensure that water is used efficiently, minimize environmental impact, and reduce operational costs. With the advancement in technology, water flow sensors have become more efficient, accurate, and easier to install and maintain. As water continues to be a valuable resource, the use of water flow sensors will remain a necessity in various industries.
A Guide to Obtaining Concentration Measurements from Common Inline Sensors
The use of common inline sensors is becoming increasingly popular in the industrial sector, particularly in applications where the control of certain components’ concentration is critical. Investment in expensive analytical equipment can place a significant financial burden on companies, but the use of comparatively affordable inline sensors can yield reliable concentration measurements. By utilizing these sensors correctly, companies can effectively monitor and regulate the concentration of key components in real-time, ensuring they meet desired specifications.Inline sensors are typically placed in the process stream to monitor various parameters, including electrical conductivity, ultrasonic waves, refractive index, and more. However, not all inline sensors are suitable for concentration measurement applications. The sensors must measure a physical parameter that directly correlates with the concentration of the component being monitored. In most cases, the physical parameter is directly proportional to the concentration and can be calibrated to provide concentration measurements.To obtain concentration measurements, the sensor must be calibrated, taking into account various characteristics such as flow rate, temperature, and pressure. Calibration is a critical process that requires precision and knowledge of the measuring system’s characteristics to ensure accurate and repeatable measurements. Companies must validate and verify the calibration process periodically to maintain measurement accuracy and quality.The calibration process involves creating a calibration curve that relates the physical parameter measurement to the concentration of the component being monitored. The calibration curve is then utilized by the sensor to calculate the concentration of the component in real-time. Utilizing appropriate sensors, such as the ones offered by the company {}, helps to ensure that the calibration process achieves the required accuracy and repeatability when determining the concentration of the component being monitored.While inline sensors can be used to accurately assess component concentration levels, there are several challenges that companies may face during their use. Companies must take into account the potential impact of the fluid matrix, which may affect the concentration measurements. In some cases, trace impurities or process fluctuations may also affect the accuracy of the inline measurements, necessitating corrective measures.Regular maintenance and calibration checks are essential in ensuring that inline sensors provide reliable measurements. Regular monitoring of the sensors’ performance can help detect drifts in the system and enable companies to maintain and verify the quality of the measurement results promptly. Monitoring also helps ensure that the sensor continues to operate within specification, and any required corrective actions can be taken promptly.It is important to note that inline sensors provide real-time measurements that can aid in process control. Effective monitoring of component concentrations can help companies avoid costly process disruptions, maintain control of their process, and ensure consistent product quality. The use of inline sensors can also help identify and diagnose issues with the process, before any significant consequences arise.In conclusion, inline sensors provide an efficient means of measuring component concentrations in real-time, enabling companies to take corrective action promptly. By utilizing reliable sensors, such as the ones offered by {}, and implementing an appropriate calibration process, companies can effectively monitor and regulate the concentration of key components, enhancing overall process control and product quality. Ongoing monitoring of measurement quality and system performance is critical in ensuring that the sensor continues to operate within specifications and maintains quality control of the process.
Find Quality Water Flow Meters and Associated Products on Ferret.com.au
Flow meters are essential devices that measure the volume of fluid that is flowing through a pipe or a system. In the world of industrial and commercial applications, flow meters are commonly used to monitor and optimize operations, ensuring that everything runs smoothly while minimizing waste and inefficiencies. One of the most common types of flow meters is the water flow meter, which is used in a wide range of applications across different industries.The importance of water flow meters cannot be overstated, especially in industries where water is a critical component of the manufacturing process. These devices help ensure that the right amount of water is used in each stage of the process, preventing wastage and reducing costs. In addition to industrial applications, water flow meters are also used in commercial and residential settings to monitor water usage and prevent excessive consumption.When it comes to choosing a water flow meter, there are several factors that must be taken into consideration. The most important of these is accuracy, as even a small error in measurement can result in significant losses or inefficiencies. Other factors to consider include the type of fluid being measured, the flow rate and pressure, and the environment in which the meter will be installed.At Ferret.com.au, we understand the importance of water flow meters in a wide range of industries, which is why we showcase products from suppliers of Flow Meter Water and other related products and services. Our platform makes it easy for businesses to find the right water flow meter for their needs, with a wide range of options to choose from.One of the suppliers featured on our platform is a global leader in the manufacturing of flow meters and other fluid measurement devices. With over 80 years of experience in the industry, this company has the expertise and knowledge to provide high-quality solutions to a wide range of customers across different sectors.Their water flow meters are designed to meet the specific needs of each customer, with a wide range of options available to ensure the best possible accuracy and performance. They offer several different types of water flow meters, including electromagnetic, ultrasonic, and vortex meters.Electromagnetic flow meters are ideal for applications where highly accurate measurement is required, and where the fluid being measured is conductive. These meters use a magnetic field to measure the flow rate, and are highly reliable and accurate.Ultrasonic flow meters are ideal for applications where non-invasive measurement is required, as they do not require any contact with the fluid being measured. This makes them ideal for applications where the fluid being measured is hazardous or corrosive.Vortex flow meters are ideal for applications where the fluid being measured contains solid particles or is highly viscous. These meters measure the flow rate based on the frequency of vortices that are created in the fluid as it flows through the meter.In addition to their water flow meters, this supplier also offers a wide range of other fluid measurement devices, including gas flow meters, level sensors, and pressure transmitters. They also offer a range of services, including installation, calibration, and maintenance, to ensure that their customers get the best possible performance from their devices.At Ferret.com.au, we are committed to connecting businesses with the best possible suppliers of Flow Meter Water and other related products and services. With our platform, customers can find the right water flow meter for their needs, with access to a wide range of options and expert advice from our team.Whether you are looking for a simple water flow meter for commercial or residential use, or a more complex device for industrial applications, we can help you find the perfect solution. With our platform, you can ensure that your operations run smoothly and efficiently, while minimizing costs and waste. So why wait? Visit Ferret.com.au today to find the right water flow meter for your needs.
How to Measure Aquarium Water Flow with a Sensor
for Aquariums, Aquarium Water Flow Meter, Aquarium Water Top Up, and Aquarium Sea Flow Meter.Sea Water Flow Sensor for Aquariums: A Must-Have AccessoryAquarium owners would agree that proper water flow is critical for the health of fish and plants. Aquarium water flow can positively affect fish health, control algae growth, and enhance the beauty of your aquarium. A water flow meter or sensor can be a great tool to measure and monitor the water flow inside your aquarium.An aquarium water flow meter can be a valuable accessory for hobbyists who want to automate the topping up process, control the water flow, and maintain the right water parameters such as temperature, pH, and salinity. A good quality water flow meter can help prevent unexpected problems that may arise due to insufficient water flow.Sea Water Flow Sensor for Auto Water Top UpOne function of the aquarium water flow meter is to automatically top-up the aquarium water by detecting and replacing the evaporated water in the aquarium with fresh or purified water. This process is necessary to maintain the right salinity level, which can affect the health of your fish and coral.The aquarium water flow meter detects the water level inside the aquarium and connects to the aquarium’s water supply. The monitor automatically turns on the water flow when it detects a drop in the water level below the desired level, and then turns off the flow when the water level is sufficient.Sea Flow Meter Suppliers and ManufacturersWhen choosing an aquarium water flow meter, it is important to consider the type of meter that best suits your needs. There are a variety of options available on the market such as magnetic, float type, and digital meters.Magnetic meters use a magnetic field to detect the flow of water through the pipe. They are highly accurate and can be used for larger aquariums. Float type meters use a mechanism of a floating object to gauge the flow of liquid through the pipe. They are commonly used for small to medium-sized aquariums.When buying an aquarium water flow meter, it is also important to consider buying from reputable suppliers and manufacturers. They often offer better quality products, warranties, and after-sales support that can help you understand and use your aquarium water flow meter effectively.In conclusion, a sea water flow sensor can be a great tool for aquarium owners to keep their aquarium healthy, clean, and at the right water levels. By choosing the right type of meter, from reputable suppliers, and manufacturers, you can automate the process of topping up the aquarium water and create a better environment for your fish and plants.
Historic Nuclear Accident Caused by Level Sensor Malfunction in the US
headline: Three Mile Island marks 42nd anniversary of worst nuclear power plant disaster in US historyOn March 28, 1979, the Three Mile Island nuclear power plant located in Pennsylvania, USA, witnessed a catastrophic event that is still remembered as the worst nuclear power plant disaster in the history of the country. On the 42nd anniversary of the disaster, it is worth revisiting the events that unfolded on that fateful day.The TMI-2 reactor at the power plant suffered a partial core meltdown that resulted in the destruction of the reactor. The meltdown was triggered by a small malfunction in the secondary cooling circuit that allowed the temperature in the primary coolant to rise. This caused the reactor to shut down automatically.The situation worsened because the level controls turned off the coolant to the reactor when they detected the presence of cooling water near the top of the tank. The water at the top was not because of the tank being completely filled, but because the water was too little in the tank that it got boiled and swelled up to the top of the tank.The accident led to the release of radioactive gases and iodine-131 into the atmosphere, which resulted in the evacuation of nearly 140,000 people. Although no fatalities were reported due to the accident, it is estimated that the disaster caused more than $1 billion worth of damage.The primary cause of the accident was attributed to human error. The failure of the operators to recognize the anomaly in the cooling system led to a delay in shutting down the reactor, which compounded the situation further.The disaster had a major impact on the nuclear power industry in the United States. It resulted in stricter regulations and safety measures, which significantly affected the development of new nuclear power plants in the country. It also led to a shift towards alternative sources of energy, such as solar and wind power.The company that operated the TMI-2 reactor, (need remove brand name), also underwent significant changes. The disaster led to the dismantling of its nuclear power division and a focus on other areas of business.In the years following the disaster, efforts were made to address the environmental and health impacts of the accident. The cleanup of the site took nearly 14 years to complete, and the effects of the radiation exposure on the local population are still being studied.The Three Mile Island disaster remains a stark reminder of the potential risks associated with nuclear power. While significant progress has been made in improving safety measures and regulations, the risk of accidents cannot be completely eliminated.As we mark the 42nd anniversary of the disaster, it is important to remember the lessons learned from the tragedy and to continue to strive for safer and cleaner sources of energy for the future.