Quality Level Sensors for Sale - Reliable Sensor Distributor and Manufacturer in China
By:Admin
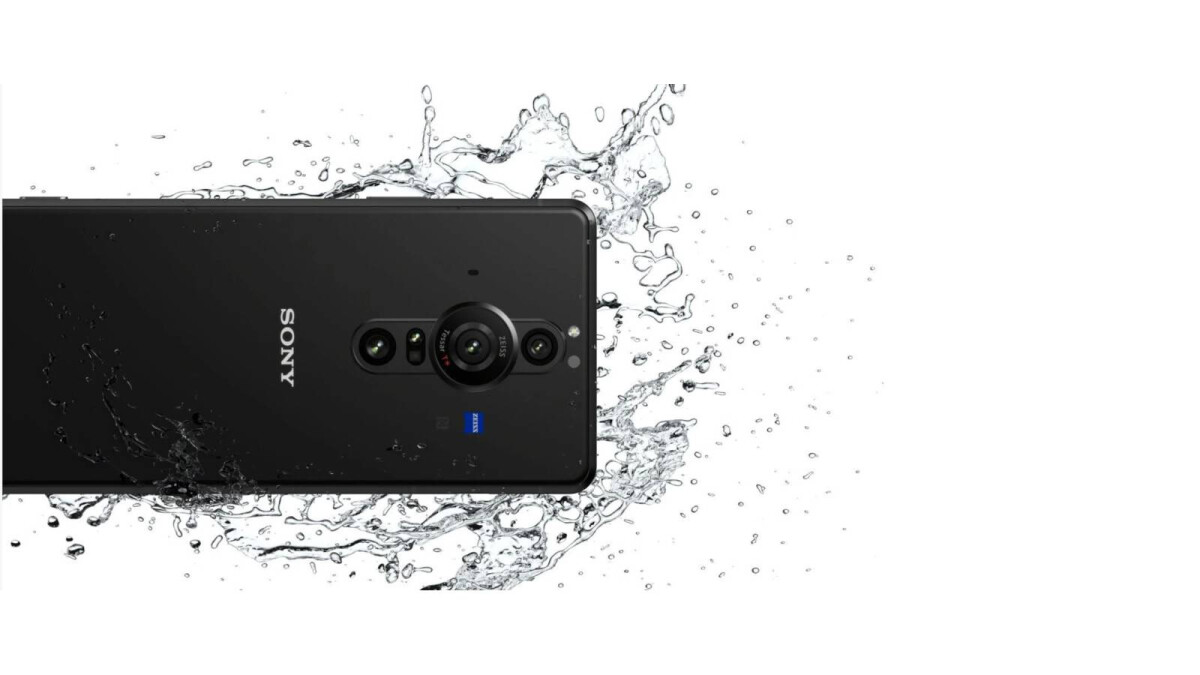
Company News & Blog
Catastrophic Accident at US Nuclear Power Plant Caused by Faulty Level Sensors
and Safety Measures for Nuclear Power Plants. Nuclear power plants are known for their reliable, clean, and safe generation of electricity. However, they are also notorious for their potential to cause accidents that can result in severe radiation exposure and contamination. One such incident took place on 28th March 1979, at the Three Mile Island nuclear power plant in the USA. The accident, which occurred in the # 2 reactor, resulted in the destruction of the TMI-2 reactor.The cause of the accident was a malfunction in the secondary cooling circuit, which allowed the temperature in the primary coolant to rise. This triggered an automatic shutdown of the reactor. However, the situation worsened when the level controls turned off the coolant to the reactor when they detected the presence of cooling water near the top of the tank. This was not because the tank was full; rather, it was because the water level in the tank was too low, causing it to boil and swell up to the top of the tank.To prevent accidents like these from happening, nuclear power plants use various safety measures, one of which is radar level sensors. These sensors are designed to continuously monitor the level of liquid in tanks and vessels, enabling real-time monitoring of fluid dynamics. They are ideal for nuclear power plants, where the accurate and reliable monitoring of fluid levels is essential for the safe operation of the plant.Radar level sensors work by sending electromagnetic waves into the tank, which reflect off the surface of the liquid and return to the sensor. By measuring the time it takes for the waves to return, the sensor can determine the exact level of the liquid in the tank. This information is then transmitted to a control system, which can automatically adjust the supply of coolant to the reactor to ensure that it remains within safe levels.In addition to radar level sensors, there are other safety measures that nuclear power plants use to prevent accidents. For example, they have redundant systems that can take over if one system fails. They also have safety protocols in place that can trigger an immediate shutdown in the event of an anomaly. Regular inspections and maintenance are also conducted to ensure that all systems are functioning correctly.In conclusion, the Three Mile Island accident, which occurred in 1979, was a sobering reminder of the potential dangers associated with nuclear power plants. Since then, significant improvements in safety measures, such as the use of radar level sensors, have made these plants much safer. However, as with any complex technology, it is essential to remain vigilant and continue to implement safety measures to prevent accidents from occurring in the future.
Efficiently measure water tank level with a pressure sensor/transducer for Pico simarine system
, Water Tank Level Sensor, Boat Tank Sensor, Marine Tank Sensor, Marine Water Tank Level Sensor.Measuring the level of water in the tank on a boat or yacht is important for several reasons. It enables the owner to know how much water is available, and when it is time to fill up the tank. A pressure sensor or transducer is an effective method of measuring the water tank level on boats or yachts.A pressure sensor for a water tank consists of a small device that is fitted inside the tank. It is connected to a monitor or display that reads the pressure changes in the water inside the tank. When the water level changes, the sensor reads the pressure difference created by the water column in the tank and sends a signal to the monitoring unit to provide the tank level readings.One of the common types of pressure sensors used for water tanks is the piezoelectric pressure sensor that uses a crystal to convert the pressure changes into electronic signals that the monitor can read. This type of sensor is durable and robust, making it suitable for use in marine environments.The Safiery Water Tank Pressure Sensor is one of the popular sensors used for water tank measurement in boats and yachts. It can be easily connected to the Pico simarine monitoring system, and it provides accurate and real-time readings of the water tank level. The sensor is designed to withstand the harsh marine environment and is resistant to corrosion and UV radiation.Other options for water tank pressure sensors for boats and yachts include the Maretron TLA100 Tank Level Adapter and the Seaboard Marine Water Tank Pressure Sensor. These sensors are also designed to withstand marine environments and provide accurate readings of the water tank level.In conclusion, using pressure sensors for water tank level measurement in boats and yachts is an effective method that provides accurate and real-time readings. There are several options for water tank pressure sensors in the market, including the Safiery Water Tank Pressure Sensor, Maretron TLA100 Tank Level Adapter, and Seaboard Marine Water Tank Pressure Sensor. It is vital to choose the one that is suitable for your specific boat or yacht requirements and to ensure that it is compatible with your existing monitoring system.
Discover the Latest Innovations in Vortex Flowmeter Technology at a Leading Factory
Vortex Flowmeter Manufacturer Revolutionizes Flow Measurement IndustryIn a groundbreaking development for the flow measurement industry, a leading vortex flowmeter manufacturer has introduced cutting-edge technology that promises to enhance accuracy and reliability. The company, which requests to remain anonymous, has set new benchmarks with its innovative vortex flowmeter, revolutionizing the way fluid flow is measured in various industries.Built on years of research and development, this vortex flowmeter offers numerous advantages over traditional flow measurement techniques. It is designed to accurately measure the flow rate of gases, liquids, and steam, making it applicable in a wide range of industries including oil and gas, chemical manufacturing, and power generation.The vortex flowmeter utilizes the vortex shedding principle, which is based on the discovery that a fluid flow past a blunt body, such as a bluff cylinder or a flat plate, creates fluctuating vortices. By strategically placing a bluff body at the center of the flow path, the flowmeter can effectively measure the frequency of these vortices and determine the flow rate.One of the key advantages of this new vortex flowmeter is its high accuracy. By leveraging advanced technology and precise calibration techniques, the company has achieved an accuracy rate of up to ±0.5% of the measured value. This level of accuracy ensures reliable and consistent readings, allowing industries to make informed decisions based on precise flow data.Furthermore, this vortex flowmeter is equipped with state-of-the-art features that optimize its performance and reliability. For instance, it incorporates a specialized signal processing algorithm that reduces interference from external factors such as vibrations, pressure fluctuations, and temperature changes. This ensures that the flowmeter provides accurate readings even in challenging operating conditions.Ease of installation and maintenance is another notable feature of this vortex flowmeter. Its compact and lightweight design facilitates straightforward installation, saving time and effort. Additionally, the flowmeter's self-diagnostic capabilities and built-in diagnostic functions allow for proactive maintenance, reducing downtime and ensuring continuous operation.The versatility of this vortex flowmeter is reflected in its wide operating range and compatibility with various piping sizes. It can reliably measure flow rates ranging from low to high velocities, making it suitable for a broad spectrum of applications.By delivering accurate and reliable flow measurements, this vortex flowmeter helps industries optimize their processes, minimize waste, and improve overall efficiency. With its exceptional performance and state-of-the-art features, it has quickly gained recognition as a game-changer in the flow measurement industry.The manufacturer behind this revolutionary vortex flowmeter boasts an impressive track record and reputation for excellence. With extensive experience in the field of flow measurement, the company is committed to continuous innovation and maintaining the highest standards of quality.In order to meet the increasing demand for this cutting-edge technology, the vortex flowmeter manufacturer has expanded its production capabilities. The company has invested in advanced manufacturing facilities, employing state-of-the-art machinery and highly skilled professionals to ensure the seamless production of these high-quality flowmeters.In addition to its commitment to innovation and quality, the manufacturer also prioritizes customer satisfaction. The company offers comprehensive technical support, ensuring that clients receive prompt assistance and guidance throughout the installation and operation of their vortex flowmeters.The introduction of this revolutionary vortex flowmeter marks a significant milestone in the flow measurement industry. With its unmatched accuracy, reliability, and versatility, it has the potential to transform how industries measure and control fluid flow. As the manufacturer continues to refine and expand its product offerings, the future of flow measurement looks promising, with increased efficiency and optimization on the horizon.
Non-Contact Radar Sensor for Accurate Bulk Solid Level Measurement
Radar Sensor: A Game Changer for Non-Contact Level Measurement of Bulk SolidsThe world is changing, and so is the way we measure things. In the field of industrial measurement, the advancement of technology has led to the development of new and more effective methods of measuring various substances, including bulk solids. One such method that has been gaining popularity in recent times is the use of radar sensors for non-contact level measurement of bulk powders, grains, and granules. VEGAPULS 69 is one such product that is aimed at providing reliable measurement values, even in the presence of buildup, caking, and vessel internals. At the heart of this product is its advanced 80 GHz technology that is capable of penetrating through various materials, including dust and water vapor, to provide accurate results. This technology is based on the principle of radio waves, which are emitted from the sensor and then reflected back by the substance being measured. The Radar Sensor then analyses the time taken for the waves to travel back and forth to determine the level of the substance present in the container. This innovative solution eliminates the need for physical contact with the substance, thereby ensuring that there is no contamination or damage to the product being measured. VEGAPULS 69 can also measure a variety of bulk solids such as plastics, sand, cement, gravel, and many others. Its sensor design also allows for easy installation onto existing containers, bins, and silos, thereby making it a cost-effective solution for industries looking to upgrade their measurement systems.One of the standout features of VEGAPULS 69 is its ability to provide reliable results even in the presence of buildup, caking, and vessel internals. This is a common problem that occurs in many industrial processes, where the substance being measured adheres to the container walls or forms lumps that can interfere with the measurement process. However, the advanced radar technology used in this product can penetrate through these materials, ensuring accurate results, even in challenging environments.Moreover, this product is capable of anti-collision detection, which means it can detect objects that come in contact with the sensor and stop the measurement process to prevent damage to either the sensor or the object. This feature ensures the longevity of the sensor and its working capabilities, thereby making it a reliable investment for any industry.As a company, we remain committed to providing innovative and dependable solutions to our customers. With VEGAPULS 69, we have taken our commitment to the next level by providing a product that meets the needs of various industries. We understand that accurate measurement of bulk solids is essential for the smooth operation of many industrial processes, and that is why we have developed this product to meet our clients' needs. In conclusion, non-contact level measurement using radar technology is a game-changer in the field of industrial measurement. VEGAPULS 69 is a product that demonstrates this innovation and its ability to provide reliable results even in challenging environments. It is a cost-effective and easy-to-install solution that can be used in various industrial processes, making it a valuable investment for any industry. Our commitment to providing our clients with dependable solutions remains resolute, and we will continue to develop and innovate to meet their needs.
Top Chinese Manufacturer with 20 Years of Experience in Silicon Pressure Sensors
: Benefits and ApplicationsPressure sensors are essential components in many industrial applications, as they help monitor and regulate pressure in a variety of environments. When it comes to silicon pressure sensors, they are among the most commonly used because of their high accuracy, low power consumption, and compact size. Silicon pressure sensors are designed to detect changes in pressure and provide an electrical output, making them ideal for use in a wide range of industries, including automotive, medical, aerospace, and manufacturing. In this article, we will explore the benefits and applications of silicon pressure sensors.Benefits of Silicon Pressure SensorsAccuracyOne of the primary benefits of silicon pressure sensors is their high accuracy. They can provide precise readings of pressure changes, making them ideal for critical applications such as aerospace and medical industries, where precision and accuracy are paramount.Compact SizeSilicon pressure sensors are also highly compact, making them easy to install in tight spaces. They are typically small enough to fit within electronic devices, which is why they are commonly used in medical devices and other portable equipment.Low Power ConsumptionSilicon pressure sensors require minimal power to function. This makes them ideal for battery-operated devices, such as wireless sensors and portable equipment, where energy conservation is important.DurabilitySilicon pressure sensors are highly durable and can withstand harsh environments. They can function in high temperatures, rugged locations, and corrosive environments without losing their accuracy. This makes them ideal for use in the automotive industry or other areas where sensors are exposed to harsh conditions.Applications of Silicon Pressure SensorsAerospace IndustrySilicon pressure sensors are widely used in the aerospace industry to monitor pressure changes in critical systems, such as fuel injection, hydraulic systems, and pneumatic systems. These sensors play a vital role in ensuring the safety and reliability of aerospace equipment.Automotive IndustrySilicon pressure sensors are used in the automotive industry to monitor fuel pressure, oil pressure, and transmission pressure. These sensors provide essential data to control engine performance, improve fuel economy, and enhance driver safety on the road.Medical IndustrySilicon pressure sensors are widely used in medical devices to monitor vital signs such as blood pressure, heart rate, and respiratory rate. Medical devices such as blood pressure monitors, ventilators, and infusion pumps use silicon pressure sensors to provide accurate and reliable data.Manufacturing IndustrySilicon pressure sensors are used in the manufacturing industry to monitor pressure changes in various processes, including chemical processing and water treatment. These sensors help control the flow of materials in manufacturing processes and maintain optimal conditions for production.ConclusionSilicon pressure sensors are versatile and durable sensors that have a wide range of applications across various industries. They provide high accuracy, low power consumption, and are compact, making them ideal for use in numerous portable devices. As technology continues to evolve, the applications of silicon pressure sensors are expected to grow, making them a critical component of modern industries.
Effective Water Flow Measurement with Clamp-On Ultrasonic Flow Meter
article on the importance of water flow sensors in various industries.Water Flow Sensor: The Importance of Measuring Water Flow RatesWater is an essential resource in our daily lives and in various industries. Maintaining a consistent water flow rate and accurately measuring it is crucial for a variety of processes. That is where water flow sensors come into play. These devices are designed to measure the rate and quantity of water flowing through pipes and channels. They are used in a range of industries, including manufacturing, agriculture, environmental monitoring, and more.Industries that require water for their processes rely heavily on water flow sensors. For instance, the food and beverage industry needs to maintain a constant flow rate of water for cleaning and sterilization purposes. Any deviation in water flow rate can lead to contamination and affect product quality. In the pharmaceutical sector, water is a critical component in drug manufacturing, and any fluctuation in water flow rates can impact the final product's quality and efficacy.Water flow sensors are also widely used in irrigation systems, particularly in agricultural practices. These sensors help farmers to monitor the water flow rate and ensure that crops are receiving the required amount of water. Overwatering can lead to wastage of water and increase operational costs, while underwatering can cause crop failure and financial losses. Water flow sensors provide precise data, enabling farmers to make informed decisions about water usage and management.The mining and construction industry also relies on water flow sensors. In mining, water is used for dust suppression and mineral processing. In construction, water flow sensors are used for concrete mixing and dust suppression. Accurately measuring the water flow rate is essential in reducing water wastage, minimizing environmental impact, and reducing operational costs.Water flow sensors are also used in environmental monitoring. They are essential in measuring river and stream flow rates, which is critical in predicting flooding risks and managing water resource allocation. Additionally, they are used in wastewater treatment plants to measure the flow rate and adjust the treatment process accordingly. This helps in ensuring that only quality water is discharged back into the environment.In recent years, the use of water flow sensors has increased, thanks to technological advancements. One of the latest developments is the clamp-on ultrasonic flow meter. This type of flow meter is non-intrusive and can be quickly installed without disrupting operations. It uses ultrasonic sound waves to measure the velocity of water flow, which is then converted into a volumetric flow rate. The clamp-on design allows for easy installation and maintenance, eliminating the need for cutting pipes or introducing any foreign materials into the water flow.In Indonesia, Wiratama Mitra Abadi is one of the leading distributors of water flow sensors, including clamp-on ultrasonic flow meters. The company has been providing high-quality instrumentation, mechanical, and automation tools since 2004. They offer a wide range of water flow sensors from various manufacturers, providing clients with a variety of options to meet their unique needs.In conclusion, water flow sensors play a crucial role in various industries and processes. They help to ensure that water is used efficiently, minimize environmental impact, and reduce operational costs. With the advancement in technology, water flow sensors have become more efficient, accurate, and easier to install and maintain. As water continues to be a valuable resource, the use of water flow sensors will remain a necessity in various industries.
How to Monitor Water Levels: A DIY Guide for Rural Living
Water shortage is a major concern in many parts of the world. Having a steady and reliable source of water is essential for daily life, agriculture, and industry. On a farm with a borehole, the water is stored in a large tank. However, if the borehole pump fails, the water supply will be cut off, and it could take some time to fix the problem. Therefore, it's important to have a warning system in place that can detect the water level in the tank and alert the owner when it's getting low. One effective solution is to use an ultrasonic water level sensor.An ultrasonic water level sensor is a device that uses sound waves to measure the distance between the sensor and the water surface. The sensor emits a high-frequency sound wave that travels through the air and reflects off the surface of the water. The sensor then measures the time it takes for the sound wave to return to the sensor and calculates the distance between the sensor and the water surface. This information can be used to determine the water level in the tank and provide an accurate reading.There are several advantages to using an ultrasonic water level sensor. First, it's a non-contact measurement method, which means that there are no sensors or probes that need to be installed in the tank. This makes installation and maintenance much easier and reduces the risk of damage to the tank or the sensor. Second, ultrasonic sensors are very accurate and can measure the water level to within a few millimeters. Third, ultrasonic sensors are very reliable and can operate in a wide range of temperatures and weather conditions.To install an ultrasonic water level sensor, you will need to mount the sensor above the water tank and connect it to a microcontroller or a smart home platform like SmartThings. The sensor can be powered by a battery or a low-voltage power supply. Once the sensor is connected, you can set up alerts to notify you when the water level is getting low. These alerts can be sent via email, text message, or push notification, depending on your preferences.In conclusion, an ultrasonic water level sensor is an effective and reliable way to monitor the water level in a tank. It's easy to install, accurate, and can provide early warning of potential water shortages. By using an ultrasonic water level sensor, you can ensure that your farm or home has a steady and reliable water supply, even in the event of a pump failure.
Top-rated Supplier and Manufacturer of Radar Level Indicators in China
Understanding Radar Level Indicators and Their Importance in IndustriesIndustries such as petroleum, chemical, food processing, and utilities require an efficient and accurate way of measuring the level of liquids and solids in various containers and tanks. This is where the radar level indicator comes in. Radar level indicators are essential instruments that help in measuring the level of liquid, solids, and sludge in tanks, vessels, and silos accurately. These instruments utilize the latest technology to deliver accurate, reliable, and real-time information about the level of fluids, liquids, and solids in storage tanks.What is a Radar Level Indicator?Radar level indicators are devices with advanced electronic systems used to measure the level of liquids and solids in tanks and silos. These instruments work by transmitting electromagnetic waves that travel down to the surface of the stored product in the tank. The electromagnetic waves reflect back to the radar level indicator's antenna, which measures the time it takes for the waves to return. This process helps determine the distance between the surface of the liquid or solid and the level sensor.Types of Radar Level IndicatorsThere are two main types of radar level indicators: Guided Wave Radar (GWR) and Non-Contact Radar (NCR). The main differences between these two types lie in their mode of operation.1. Guided Wave RadarGuided Wave Radar (GWR) level indicators work by sending high-frequency electromagnetic waves down a probe (or waveguide) inserted into the tank or vessel. The electromagnetic waves move down the probe until they reach the liquid or solid product. The waves reflect back to the probe, which measures the time it takes for the waves to return. This data helps determine the level of product in the tank.GWRs are versatile and can measure the level of a wide range of liquids and solids, from water to molten metal. They are also suitable for high-temperature and high-pressure applications.2. Non-Contact RadarNon-Contact Radar (NCR) level indicators use a horn antenna to send out electromagnetic waves towards the product's surface. The waves penetrate the product, reflect back to the antenna and are then measured. NCRs are ideal for measuring the level of substances that are not conductive, such as powders and solids.Benefits of Using Radar Level Indicators1. Increased efficiencyRadar level indicators provide a real-time view of the level of product in the tank or vessel. This data helps operators to maintain the optimum level of product, reducing overfilling or underfilling.2. Improved Safety and Environmental ProtectionOverfilling of tanks and vessels can lead to catastrophic consequences, such as spills, which can result in environmental degradation and accidents. Radar level indicators provide reliable and real-time information that can help prevent these situations.3. VersatilityRadar level indicators are versatile and can measure the level of a wide range of liquids and solids, from water to molten metal. This ensures that industries can use the instruments in various applications.4. Cost SavingsIndustries that use radar level indicators can save on costs associated with material waste and production downtime. Operators can also reduce equipment damage due to overfilling and avoid costly repairs.ConclusionRadar level indicators are essential instruments that provide accurate and reliable measurements of the level of liquids and solids in tanks, silos, and vessels. Industries can use these devices in various applications, thus ensuring efficient product management. Additionally, radar level indicators promote environmental protection and safety by preventing overfilling of tanks and vessels. Investing in radar level indicators can lead to increased efficiency, reduced costs, and improved safety in industries.
Namulonge to Host Farm Clinic for Agriculture Experts and Farmers to Discuss Industry Challenges
As the world's population continues to expand, the pressure on the agriculture industry to produce more food grows. Farmers are constantly looking for solutions to increase crop yields and improve the quality of their produce. However, the challenges they face can be overwhelming. Soil acidity, pests and diseases, and changing weather patterns are just a few of the issues that affect crop production. To address these challenges, experts and farmers are coming together at the Seeds of Gold Farm Clinics held at Namulonge.The Seeds of Gold Farm Clinics have become a vital forum for experts and farmers to share information and find solutions to the most pressing problems facing the agricultural industry. These clinics provide an opportunity for farmers to learn from experienced agriculturalists about the latest innovations in crop production. One of the key issues farmers face is soil acidity. To address this, the experts at the Farm Clinics share insights on how to measure soil pH levels and how to treat acidic soils with the right materials.Monitoring soil pH is crucial because the acidity of soil affects the plant's ability to absorb nutrients. Soil with a pH level that is too high or too low can negatively impact crop yield and plant health. The pH level of the soil is the measure of its acidity or alkalinity. Generally, soils with a pH level between 6.0 and 7.5 are suitable for most crops. However, different crops have different soil pH requirements, and farmers need to understand these requirements to maximize their yields.The experts at the Seeds of Gold Farm Clinics teach farmers how to use pH monitors to measure soil acidity. These monitors provide accurate soil pH readings that help farmers determine if their soil is too acidic or alkaline. They also help farmers to find the right balance of nutrients for their crops and identify nutrient deficiencies. The use of pH monitors is becoming increasingly popular among farmers because they are easy to use and provide fast and accurate results.Farmers attending the Seeds of Gold Farm Clinics also learn about the different methods of treating acidic soils. One way to treat acidic soils is to add lime or other materials that can neutralize soil acidity. Another approach is to use fertilizers that contain calcium and magnesium to raise the pH level of the soil. Farmers are advised to test their soil before applying any treatment, to avoid soil over-correction and imbalances of nutrients.By attending the Seeds of Gold Farm Clinics, farmers gain access to the latest research and expert advice on the best crop management practices and solutions for issues like soil acidity. The Farm Clinics have been instrumental in helping farmers improve their crop yields and quality while also preserving the ecosystem. One farmer who attended a Seeds of Gold Farm Clinic shared that "I have learned a lot about soil acidity and how to monitor and treat it. The knowledge I have gained has enabled me to increase my maize yields by thirty percent."In conclusion, the Seeds of Gold Farm Clinics are a must-attend forum for farmers looking to improve their crop yields and quality. The clinics provide an opportunity for farmers to learn from experts about the latest innovations in crop production and management, including monitoring soil pH levels. With the knowledge and skills gained from the Farm Clinics, farmers can improve their productivity, reduce the impact of pests and diseases, and ensure food security for the growing population.
Innovative Pressure Sensor With Displacement Sensor and Elbow Pipe
, Pressure Sensing Technology, Elbow Pipe Sensor, Displacement Sensor, Base, Reflection Members, Deformation, Change of Pressure, Magnitude Measurement.Pressure sensors are critical components of many industrial applications, including measuring fluid and gas pressure in a pipeline. In order to accurately measure pressure, a sensitive and reliable sensor is necessary. That's where the pipe pressure sensor comes into play.At its simplest, a pressure sensor translates pressure changes into electrical signals. The signals are then processed and used for various purposes such as controlling automated equipment, monitoring pressure levels, or providing feedback for safety systems. The pipe pressure sensor is a special type of pressure sensor that is installed directly on an elbow pipe.The pipe pressure sensor comprises three essential components: a displacement sensor, an elbow pipe, and a base. The elbow pipe's first end is fixed on the base, and the displacement sensor is fixed on the base too. The displacement sensor comprises two reflection members; the first is fixed in the main body of the displacement sensor, and the second is movable relative to the main body of the displacement sensor.The second reflection member is connected to the elbow pipe at a first position of the elbow pipe, or alternatively, it is fixed on the base, and the main body of the displacement sensor is connected to the elbow pipe at a first position of the elbow pipe. When the pressure in the elbow pipe changes, the elbow pipe deforms, causing a change in the distance between the first reflection member and the second reflection member. The amount of deformation is measured by the displacement sensor, and the magnitude of the change in pressure is obtained from this measurement.By using an elbow pipe sensor, it's possible to obtain highly accurate measurements of pressure in a pipeline. Elbow pipes are a common feature in many industrial setups. They allow for a change in the direction of flow while reducing turbulence. They are also relatively easy to install and maintain, making them a cost-effective solution.Pressure sensing technology has come a long way in recent years, and the development of displacement sensors has revolutionized the way in which we monitor and control pressure in pipes. The accuracy and sensitivity of these sensors have improved significantly, making them ideal for use in a wide range of applications.Choosing the right pressure sensor for your application is critical. Factors such as pressure range, temperature range, and process compatibility must be considered. Luckily, there is a wide range of options available on the market, making it easier for industries to find the right pressure sensor for their specific needs.In conclusion, the pipe pressure sensor is an essential component in many industrial processes. It enables us to measure pressure accurately and reliably, ensuring that production runs smoothly and safely. From the displacement sensor and elbow pipe to the base and reflection members, each part plays a crucial role in the functioning of this device. As technology continues to advance, we look forward to seeing even more sophisticated pressure sensing solutions in the future.